Le Maroc, un pays confronté à un risque élevé de stress hydrique, doit adopter des stratégies innovantes pour faire face à la pénurie d’eau. Le traitement des eaux usées, associé à la valorisation des boues, constitue une approche intégrée pour améliorer la gestion des ressources en eau et promouvoir une agriculture durable. Cet article propose une analyse diagnostique du traitement des boues dans les stations d’épuration. Les boues non traitées peuvent contenir des pathogènes, des métaux lourds, des produits chimiques toxiques et d’autres contaminants. Lorsque ces boues sont rejetées dans les cours d’eau ou les réservoirs, elles peuvent contaminer l’eau potable et altérer sa qualité. L’étude se concentre sur trois étapes clés du traitement des boues : l’épaississement, la digestion et la déshydratation. La méthodologie diagnostique utilisée permet de détecter les failles dans chaque procédé et vise à identifier les points d’amélioration potentiels, tout en proposant des solutions pour optimiser le traitement des boues. Mots-clés : stress hydrique, pénurie, boues, traitement tertiaire, eaux usées, qualité, analyse, pathogènes, métaux lourds, produits chimiques toxiques, contaminants, épaississement, digestion, déshydratation, optimisation.
INTRODUCTION
Les eaux usées passent par une série de traitements séquentiels en trois étapes, généralement appelées primaire, secondaire et tertiaire [1,2]. En raison de la pénurie de sources d’eau et de ses conséquences critiques [3,4] le besoin de récupération de l’eau est de plus en plus important. La problématique du rejet de boues sans traitement, ainsi que leur accumulation dans le milieu naturel représente un défi environnemental complexe. Lorsque les boues issues des stations d’épuration sont rejetées sans traitement, elles peuvent s’accumuler dans les sols et les eaux, entraînant une pollution progressive et potentiellement grave.
Ces boues contiennent souvent des contaminants tels que des métaux lourds, des pathogènes et des substances chimiques [5,6], qui peuvent altérer la qualité des sols, des nappes phréatiques et des écosystèmes aquatiques. L’accumulation prolongée de ces boues contribue également à la dégradation des habitats naturels et peut nuire à la biodiversité. Le traitement tertiaire est la dernière étape du traitement des eaux usées, qui consiste à traiter les boues. Il s’agit d’une étape supplémentaire qui vise à améliorer encore la qualité de l’eau [7,8]. Parmi les aspects essentiels du traitement des boues, l’épaississement, la digestion et la déshydratation des boues.
L’épaississement, qu’il soit statique ou dynamique, sert à concentrer les boues, recevant les extractions de boues secondaires avantmélange avec les boues primaires en vue du traitement ultérieur, il réduit le volume initial liquide et augmente la concentration de solides d’environ 1 % à 2-10 % [9]. Tandis que la digestion, aussi appelée méthanisation [10], permet de stabiliser les matières organiques, de réduire le volume des boues et les transformer en biogaz [11]. Enfin, la déshydratation est une étape essentielle pour réduire le volume des boues finales [12]. Nous nous focaliserons sur la déshydratation mécanique, y compris la centrifugation et la filtration à bandes, qui exploitent respectivement la force centrifuge et la filtration sous pression pour séparer l’eau des solides [13].
MATÉRIELS ET MÉTHODES
Afin d’assurer le bon fonctionnement d’un procédé, il est essentiel de prendre en compte divers paramètres de vérification et de dimensionnement.
Paramètres clés de vérification et de dimensionnement : Epaississeur
L’épaississeur soit dynamique ou statique, repose sur la validation de certains paramètres essentiels comme: le taux de capture, la charge surfacique et le temps de séjour. Le taux d’élimination des matières sèches, calculé à l’aide de la formule suivante, influence directement l’efficacité globale du processus de digestion:

Avec: MS influente: concentration de matières sèches dans les boues entrantes (en kg MS/m³) MS effluent: concentration de matières sèches dans les boues sortantes (en kg MS/m³) Le taux d’élimination des MS se concentre sur la quantité de matières sèches retirées du système. Le taux de capture de la matière sèche d’un épaississeur mesure son efficacité à concentrer les solides en réduisant l’eau. Un taux élevé (90-95 % idéalement) signifie une meilleure concentration des solides et moins de volume de boues [14]. Le taux de capture est calculé par cette formule:

Le taux de capture évalue l’efficacité de l’épaississeur à concentrer les solides en diminuant le volume d’eau. Le temps de séjour typique qui définit le rapport entre le volume des épaississeurs et le débit journalier de boues introduites, est de 1 à 2 jours [15,16]. Pour un épaississeur statique la charge surfacique exprimée en Kg de matières sèches par mètre carré et par jour (Kg MS/m².j), est calculée par l’équation suivante:
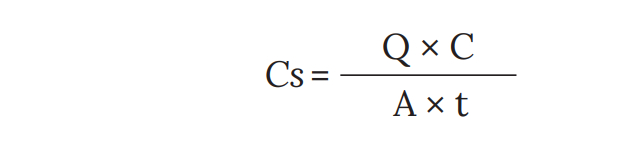
où:
Q = Débit d’alimentation en boues (m³/j)
C = Concentration en matière sèche des boues (kg MS/m³)
A = Surface de l’épaississeur (m²)
t = Temps de séjour (j)
Cette charge varie selon le type de boues. Pour les boues primaires elle se situe généralement entre 75 et 120 Kg MS/m².j, pour les boues mixtes, elle est comprise entre 45 et 75 Kg MS/m².j et finalement pour les boues secondaires (biologiques), la charge surfacique est entre 25 et 35 Kg MS/ m².j [15]. Pour assurer l’efficacité d’un épaississeur dynamique, il ne faut pas dépasser une charge surfacique de 100 Kg MS/m².j, afin de maintenir une performance optimale. En parallèle, pour améliorer le processus de séparation des particules en suspension du liquide, des polymères sont souvent utilisés.
Le dosage recommandé pour ces polymères est supérieur à 2 kg PE/T MS. De plus la pression de pressurisation est généralement contrôlée pour optimiser l’efficacité de la séparation des solides et du liquide. Elle est comprise entre 4 et 5 bars [13]. L’épaississeur dynamique basé sur le principe de flottation présente l’avantage de ne soumettre le système à aucune contrainte géométrique, contrairement à l’épaississeur statique, qui impose des contraintes spécifiques. Une hauteur de 3,5 à 4 mètres est préconisée pour le bassin de décantation, en tenant compte du volume de stockage, afin de faciliter le tassement de la boue [16]. La pente du fond doit être maintenue entre 10 % et 20 % et le diamètre inférieur varie de 7 à 30m.
Digestion
Le bon fonctionnement du digesteur est assuré si le rendement d’élimination des matières en suspension (MES) dépasse 40 % et si la concentration en méthane du biogaz produit est supérieure à 50 % [13]. Le taux d’élimination des MES se calcule selon:

Avec:
MES influente: Concentration en MES dans les boues entrantes en (en kg MS/m³)
MES effluente: Concentration en MES dans les boues sortantes en (en kg MS/m³)
Pour chaque kilogramme de matière organique (MO) traitée, la production de biogaz est d’environ 0,9 à 1,1 mètres cubes. Pour calculer la production totale de biogaz en fonction de la matière organique traitée, vous pouvez utiliser la formule suivante:

La charge volumique doit respecter un ratio de 1 ≤ Cv ≤ 4 kg MS/m³.j selon le type de boues fraîches, elle est donnée par l’expression suivante:

Où:
Cv: Charge volumique exprimée en kg MS/m³.j
Q: Débit de boues (m³/j)
MS: Concentration de matières sèches influente (kg MS/m³)
V: Volume du digesteur (m³)
La température doit être maintenue autour de 35°C [16]. Le pH optimal se situe entre 6 et 8 et peut être ajusté par l’ajout de soude ou de bicarbonate de sodium; des variations de pH peuvent perturber le processus. Le rapport entre les Acides Gras Volatils (AGV) et l’Alcalinité Totale (TAC), doit être compris entre 0,2 et 0,4. Le temps de séjour hydraulique recommandé est de 1 à 2 jours. Enfin, une seule contrainte géométrique doit être respectée: le diamètre du digesteur doit être inférieur à 35 mètres.
Déshydratation :
La déshydratation mécanique des boues est la méthode préférée en raison de sa simplicité, de sa faible consommation d’énergie [17], de ses coûts réduits et de sa flexibilité. Ce type de déshydratation repose sur des processus physiques plutôt que chimiques pour réduire le volume d’eau dans les boues [18]. Les méthodes mécaniques couramment utilisées sont les filtres à bandes et la centrifugation. Les filtres à bandes sont conçus pour atteindre une siccité minimale de 20 % [16], ce qui signifie que le taux de solidification ou de déshydratation des boues est significatif. La siccité est représentée par la relation suivante:

La filtration est effectuée à l’aide de bandes filtrantes sur lesquelles les boues passent sous pression. La pression de lavage, réglée entre 4 et 6 bars, aide à extraire le liquide restant. La vitesse de la toile, ajustable entre 1 et 5 mètres par minute, permet de réguler le débit et l’efficacité de la filtration. En outre, des polymères sont souvent utilisés pour améliorer l’agglomération des particules en suspension, facilitant ainsi leur séparation du liquide et optimisant le rendement du filtre.
La centrifugeuse offre également des performances optimisées lorsqu’elle est réglée correctement. La vitesse du bol de la centrifugeuse est généralement exploitée à environ 85-90 % de la vitesse maximale de l’équipement, ce qui permet d’assurer une séparation efficace des solides et des liquides. La vitesse différentielle (Vr), qui est régulée par le couple de la machine, joue un rôle important dans l’évacuation des solides. La vitesse de convoyage ajustable, entre 1 et 5 tours par minute, est modifiée en fonction du couple pour maintenir un fonctionnement optimal.
RÉSULTATS ET DISCUSSION Organigrammes de diagnostic
L’organigramme des boues relatifs à l’épaississeur expose l’approche diagnostique adoptée, en détaillant les étapes clés du processus et les critères d’évaluation utilisés pour optimiser l’efficacité du traitement.
Organigramme 1 : Organigramme de l'épaisseur
Dans notre étude sur le traitement des boues épaissies, le choix entre les procédés statique et dynamique dépend principalement du pourcentage de matières sèches et du taux de capture (TC). Un TC supérieur à 95 % permet de continuer sans ajustements majeurs. Si le TC est inférieur, il faut évaluer et ajuster divers paramètres. Pour les épaississeurs statiques, des problèmes peuvent apparaître si la charge surfacique ou le temps de séjour est incorrect.
Cela nécessite des ajustements des débits et éventuellement l’ajout de floculant. La détection de méthane indique la nécessité d’un chaulage, et un voile de boues faible requiert des réajustements ou, si nécessaire, l’installation d’un système de raclage ou l’ajout d’un épaississeur supplémentaire. Pour les épaississeurs dynamiques, il est crucial de vérifier le TC, la charge surfacique, et la concentration des matières sèches.
Des ajustements doivent être faits si les conditions ne sont pas respectées, notamment en ce qui concerne le dosage de polymère et la pression de pressurisation, pour maintenir l’efficacité du processus. L’organigramme suivant présente une approche simplifiée du diagnostic d’un digesteur. Il vous guidera à travers les étapes clés pour identifier les problèmes potentiels, analyser leurs causes et mettre en œuvre des solutions correctives.
Organigramme 2: Organigramme de digesteur anaérobie
En passant au second procédé qui est la digestion, les problèmes peuvent survenir si le rendement d’élimination des matières en suspension (MES) ou la concentration en méthane du biogaz ne sont pas conformes. En cas de non-conformité, il est crucial de vérifier la charge volumique, d’assurer une régularité de l’alimentation, d’ajuster le débit des boues, et de contrôler la qualité des boues primaires et secondaires. Il est essentiel d’examiner le pH afin de détecter une acidose ou une alcalose, et d’ajuster en conséquence en utilisant NaOH, en modifiant le débit, ou en diluant les boues. Il est également important de vérifier le rapport entre les acides gras volatils (AGV) et l’alcalinité totale (TAC) et d’appliquer les mesures correctives nécessaires, telles que l’ajustement du débit ou l’ajout de NaOH. La taille appropriée du digesteur est cruciale, tout comme le réglage de la température de l’eau chaude et de l’intensité du brassage pour prévenir la surchauffe des boues.
Enfin, la régulation de la température des boues, par l’ajustement du débit de recirculation, du temps de séjour, et le contrôle du calorifugeage du digesteur, est fondamentale pour garantir l’efficacité du traitement. L’organigramme suivant présente une approche méthodique pour identifier la cause des problèmes rencontrés lors de la déshydratation mécanique des boues. Pour le diagnostic du procédé de déshydratation des boues, que ce soit par centrifugation ou par filtres à bandes, le processus commence par vérifier la siccité des boues et le taux de capture (TC). Une siccité supérieure à 20 % et un TC au-delà de 97 % sont essentiels pour une déshydratation réussie.
En cas de non-conformité, il est nécessaire d’ajuster les paramètres de centrifugation, notamment la vitesse du bol et le débit des boues, et d’augmenter le dosage de polyélectrolytes, en se basant sur des tests JarTest pour optimiser le choix et la quantité de polymère. Si le TC reste insuffisant, un dosage plus élevé de polyélectrolytes peut être nécessaire. Pour les filtres à bandes, il convient d’ajuster la vitesse de la toile, le niveau de colmatage, la pression de lavage et le débit pour améliorer la siccité. Comme avec la centrifugation, des ajustements du dosage de polyélectrolytes et des tests supplémentaires peuvent être requis pour atteindre les objectifs de déshydratation.
Organigramme 3: Organigramme de la centrifugeuse et des filtres à bandes
Utilisation de Visual Studio dans le Processus de Développement
Le raisonnement basé sur les organigrammes est appliqué dans Visual Studio, un puissant outil de gestion de base de données où les résultats sont projetés. Après la saisie des éléments, Visual Studio effectue les diagnostics nécessaires pour garantir leur applicabilité. Si les conditions sont remplies, des instructions claires ou des mesures correctives sont affichées directement dans une boîte de dialogue.
Codes de base de données et d’application
Code d’application pour épaississeur
En utilisant l’algorithme fondé sur l’organigramme, l’application permet un diagnostic précis en analysant les données d’entrée pour détecter les anomalies, en effectuant des calculs de performance pour estimer le volume de boues épaissies et en fournissant des recommandations pour optimiser le fonctionnement des épaississeurs, tant statiques que dynamiques. Le code intègre des modules de visualisation permettant de suivre en temps réel les principaux paramètres de performance des épaississeurs de boues, tels que le pourcentage de matières sèches et le taux de capture.
Il permet d’évaluer les ajustements nécessaires en fonction des conditions d’opération. Pour les épaississeurs statiques, il détecte les problèmes associés à la charge surfacique ou au temps de séjour, ce qui peut nécessiter des ajustements de débit ou l’ajout de floculant. Concernant les épaississeurs dynamiques, il souligne l’importance de contrôler les paramètres essentiels afin de garantir l’efficacité du processus. Code d’application pour digesteur Le code d’application pour digesteur présenté dans la figure suivante, permet de surveiller et de contrôler les paramètres essentiels garantissant ainsi un fonctionnement optimal.
L’algorithme de base utilise les paramètres définis par l’utilisateur en conjonction avec les conditions citées dans l’organigramme préétabli. Le code comporte l’ensemble des paramètres de vérification (rendement d’élimination des matières en suspension et la concentration en méthane du biogaz) et de dimensionnement (taille du digesteur). Des ajustements du pH, ainsi que du rapport entre les acides gras volatils et l’alcalinité totale, sont également représentés en code.
Figure 1: Code d’application pour épaississeur (Thickener).
Figure 2: Code d’application pour digesteur (Digester).
Code d’application pour déshydratation (centrifugation, filtres à bandes)
Le Code d’application pour déshydratation, incluant la centrifugation et les filtres à bandes, est destiné à optimiser le processus de séparation des solides et des liquides dans le traitement des boues. Grâce à une interface utilisateur conviviale, il facilite l’entrée des données et la visualisation des performances, tout en fournissant des recommandations pour ajuster les conditions de fonctionnement. Le code débute par la vérification de la siccité des boues et du taux de capture (TC), avec des seuils critiques à respecter pour garantir une déshydratation efficace.
En cas de non- conformité, le code propose des ajustements à la vitesse de centrifugation, au débit des boues, et recommande d’augmenter le dosage de polyélectrolytes, en se basant sur des tests JarTest. Pour les filtres à bandes, il inclut des recommandations pour ajuster la vitesse de la toile, la pression de lavage et le débit, afin d’optimiser la siccité. Grâce à cette approche automatisée, les opérateurs peuvent facilement appliquer des corrections et améliorer l’efficacité du processus de déshydratation.
Figure 3: Code d’application pour déshydratation (Dewatering).
Tests et débogage de l’application :
L’interface conçue pour la saisie des données est essentielle pour tester, calculer et identifier les valeurs anormales qui pourraient provoquer des dysfonctionnements. Les illustrations ci-dessous présentent une série de tests réalisés pour s’assurer du bon fonctionnement de l’application. Les tests illustrés précédemment ont pour but de certifier de manière exhaustive la fonctionnalité de l’application et son aptitude à détecter avec précision les anomalies. Structurés autour de plusieurs critères fondamentaux, ils évaluent l’exactitude de la détection des anomalies par rapport aux valeurs théoriques et aux seuils établis. Ces tests visent à attester de la fiabilité du diagnostic fourni par l’application et de sa capacité à identifier les causes réelles des dysfonctionnements.
Figure 4: Test de débogage pour épaississeur.
Figure 5: Test de débogage pour digestion.
Figure 6: Test de débogage pour déshydratation des boues.
CONCLUSION
Ce travail a permis de développer et d’implémenter un code de diagnostic automatique spécifiquement conçu pour le traitement tertiaire des boues. L’intégration de ce code dans l’environnement Visual Studio offre une plateforme robuste et efficace pour la gestion des paramètres critiques tels que le débit, le pH, la température, ainsi que les charges surfacique et volumique lors des processus d’épaississement, de digestion et de déshydratation des boues. Grâce à l’utilisation d’organigrammes détaillés pour décrire les paramètres à surveiller, nous avons pu concevoir un système de diagnostic capable d’optimiser les performances des traitements et de garantir leur conformité avec les normes de qualité.
La mise en œuvre réussie de ce code de diagnostic automatique marque une avancée significative dans l’automatisation et l’optimisation des méthodes de traitement des boues. Ce système ne se contente pas de surveiller les conditions opérationnelles en temps réel, mais il fournit également des outils analytiques permettant d’ajuster les paramètres pour améliorer l’efficacité du traitement. Cette approche non seulement facilite la gestion des boues mais aussi réduit les risques d’erreurs humaines, offrant ainsi une meilleure fiabilité et une amélioration de l’efficacité globale du traitement.