Les sécheurs thermiques connaissent un développement soutenu depuis les années 2000. Cette solution thermique permet de réduire considérablement la masse des boues, permettant de passer d’une boue déshydratée à 20-25%MS à une boue sèche à 90%MS, tout en autorisant une valorisation agricole ou une valorisation thermique. Le Groupe SUEZ exploite en France depuis 2003 des sécheurs thermiques de différentes technologies. Pour accompagner les opérateurs de ces nouveaux équipements et capitaliser les retours d’expérience utiles pour une bonne maitrise opérationnelle et l’amélioration des installations, la Direction Technique de SUEZ Eau France a constitué en 2007 un groupe, le GEST (Groupe d’Exploitants de Sécheurs Thermiques), ouvert aux exploitants des différents sites équipés, aux représentants de SUEZ Traitement de l’eau (construction) et au CIRSEE en charge de l’expertise et de l’appui technique. Fin 2015, le Groupe SUEZ exploite 39 sécheurs répartis sur 27 sites. Les principaux problèmes et difficultés auxquels sont confrontés les exploitants concernent majoritairement les équipements périphériques du sécheur. L’objet de cet article, à partir de l’ensemble des informations recueillis par le GEST, est de proposer une analyse critique des installations, d’identifier les points de vigilance et de définir les bonnes règles de conception d’un atelier de séchage thermique des boues qu’il conviendrait de respecter lors de nouveaux projets pour fiabiliser la filière de traitement des boues et garantir les conditions de sécurité des opérateurs.
Cet
article ne décrit pas les différentes technologies de sécheur thermique pouvant
être mises en place, seuls les équipements périphériques qui constituent un
atelier global de séchage thermique sont ici abordés.
Schéma d’un atelier
de séchage thermique avec ses principaux équipements périphériques
Le
schéma suivant présente l’ensemble des périphériques constitutifs d’un atelier
de séchage :
.jpg)
Schéma
global des différents équipements périphériques d’un atelier de séchage
thermique de boues urbaines.
Les équipements implantés
en amont d’un sécheur thermique
-
Trémie tampon des boues
déshydratées
Le
premier équipement que l’on trouve en amont d’un sécheur thermique est la
trémie de stockage des boues déshydratées, couplée au système d’alimentation du
sécheur. Le volume de la trémie est à déterminer en fonction du mode de
fonctionnement du sécheur. Il importe de prévoir un tampon de quelques heures
pour pouvoir intervenir sur la pompe d'alimentation en cas de panne. Des
trémies à parois verticales sont à privilégier pour limiter les phénomènes de
voûtage. Les trémies intermédiaires sont à éviter car elles peuvent changer la
rhéologie de la boue : des phénomènes de couches d’eau et de boue peuvent
apparaître perturbant par la suite le fonctionnement du sécheur.
La
trémie de stockage des boues déshydratées doit être instrumentée afin de
pouvoir réguler le niveau de boue et assurer une alimentation continue du
sécheur, et parfois du système de dévoûtage. Les sondes doivent être
adaptées : sondes de niveau à ultrasons et trémie sur pesons. Il faut également
prévoir un piquage dans la trémie d'alimentation en amont du sécheur afin de
pouvoir prélever des échantillons de boue représentatifs.
Il
est impératif de disposer d’un point d’eau à proximité de la trémie pour le
lavage de ces équipements.
-
Pompes
d’alimentation en boue du sécheur
Les
pompes d’alimentation en boue déshydratée d’un sécheur sont généralement des pompes
à piston ou à rotor excentré. De plus la mise en place d’une grille de contrôle
visuel de l’alimentation de la pompe permet à l’exploitant de connaître
rapidement la situation.
Lorsqu’une
installation est construite sur plusieurs niveaux, il faut prévoir des
conduites de vidange manuelle en particulier dans les étages, et si possible les
diriger vers les bennes de stockage de boue.
Les
caractéristiques hydrauliques des circuits de transfert de boue sont prises en
compte pour le dimensionnement des équipements, on évite par exemple les trop
grandes distances de pompage, et on évite des diamètres de canalisation ou des
rayons de courbure de coudes trop petits (rayon de courbure des canalisations à
mettre en place R > 5D).
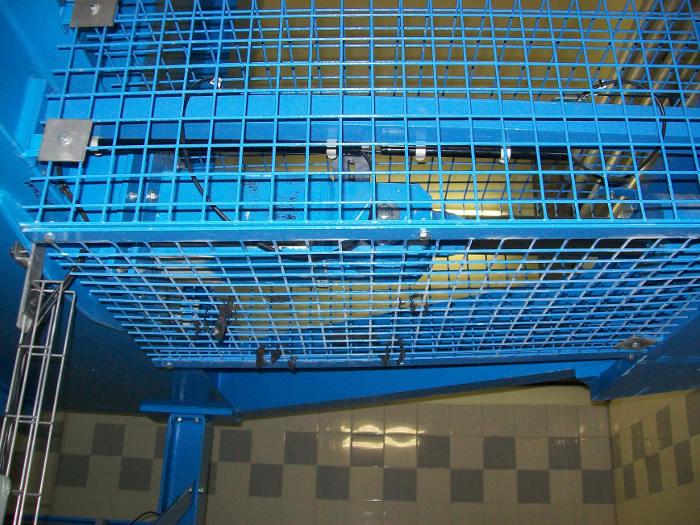
Les équipements implantés en aval d’un sécheur thermique
Traitement des buées et des incondensables :
Quelle
que soit la technologie de séchage mise en place, un mélange d'air et de vapeur
d'eau pollué par des poussières, des composés organiques volatils (COV) et de
l'ammoniac est extrait du sécheur durant son fonctionnement. Le degré de
pollution de ce mélange dépend de la température à l'intérieur du sécheur, des
volumes d’air mis en jeu, ainsi que du temps de séjour et de la nature de la
boue. Le traitement des effluents gazeux sera adapté au procédé de séchage.
Selon
le type du sécheur, ce traitement inclut :
- La séparation
des granulés secs et de la poussière (équipements de type cyclone, polycyclone,
filtre à manche ou scrubber) pour les sécheurs mixtes (VOMM), ou à tambour (DDS
d’Andritz) ;
- Le
refroidissement et la condensation de la vapeur d'eau ;
Dans
la plupart des cas, les buées chaudes sont condensées dans une colonne de
condensation sur anneaux Raschig ou par simple pulvérisation en circuit ouvert.
Dans
ce dernier cas, l'eau industrielle utilisée pour le refroidissement des buées
chaudes est généralement de l'eau traitée de la station d'épuration. Les
exploitants du GEST indiquent que plusieurs ateliers de séchage présentent une
carbonatation importante dans les condenseurs et les tuyauteries de sortie. Ces
carbonatations entraînent toujours des contraintes importantes en exploitation
(arrêt de tout l'atelier, nettoyages difficiles...). Certains condenseurs
peuvent présenter aussi des développements biologiques.
Pour
éviter ces phénomènes, en fonction de la qualité de l’eau industrielle utilisée
pour la condensation (pH, Titre Hydrotimétrique (TH) et Titre Alcalimétrique
Complet (TAC)), plusieurs solutions peuvent être mises en place :
- - Adoucir
l’eau industrielle,
- - Utiliser
des produits antitartres ;
- - Acidifier
l’eau industrielle,
- - Mettre
en place un condenseur en circuit fermé (refroidissement sur l’eau de
condensation),
-
Dans
le cas de développements biologiques, la soude ou la Javel pourront être
utilisées.
Les
recommandations des exploitants du GEST pour des buées issues des sécheurs sont
de :
- Privilégier
un système de décolmatage au-dessus du condenseur des buées pour faire une
chasse fréquente,
- Privilégier
des canalisations de type PEHD et prévoir sur les canalisations horizontales
des points bas pour les purges,
- Effectuer le plus tôt possible en sortie de sécheur la condensation des buées,
- - Rendre accessibles le condenseur et les tours de lavage pour permettre un nettoyage fréquent.
- La désodorisation de l'air avant rejet à l’atmosphère
En
fonction du type de sécheur, de la qualité des boues à sécher, et des objectifs
de réduction des odeurs, une unité de désodorisation dédiée peut-être privilégiée.
Sinon, les incondensables sont généralement envoyés vers l’unité de
désodorisation de la station.
- Refroidissement des boues séchées
En
fonction des technologies de séchage mises en place, les boues peuvent sortir
du sécheur à des températures élevées, parfois 80 à 90°C. Il est impératif de
refroidir les boues séchées avant leur stockage afin de limiter les risques
liés à l’auto-échauffement. Certains sécheurs permettent d’obtenir en sortie de
sécheur des boues séchées ayant une température suffisamment basse pour être
directement stockées (cas de l’Evaporis™ LE avec le sécheur INNOPLANA où les
boues séchées sortent à 35, 40°C au maximum). La plupart des sécheurs thermiques
nécessitent un système de refroidissement des boues séchées afin de pouvoir
être stockées de manière sécurisée.
Le
système le plus fréquemment rencontré est la vis ou bi-vis de refroidissement.
On rencontre également des refroidissements par bande transporteuse. Dans ce
cas de l’air froid est soufflé sur les boues pour les refroidir.
La
principale recommandation pour les systèmes à vis de refroidissement concerne
la ventilation. C’est en effet un point très important car en cas de mauvais
dimensionnement, des risques importants de condensation peuvent se produire
dans la vis/bi-vis, perturbant de manière considérable le fonctionnement de cet
échangeur indirect et pouvant entrainer des blocages.
Le
système de refroidissement peut servir de moyen de transport de la boue séchée
jusqu’au point de stockage. Cependant, en fonction des configurations
d’installation et/ou de l’encombrement disponible, il est parfois utile de
mettre en place d’autres technologies de convoyage après le système de
refroidissement des boues séchées.
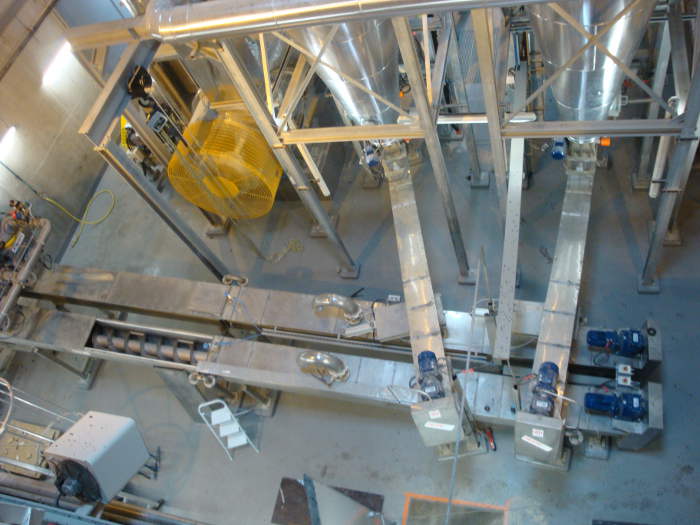
Deux vis de refroidissement des boues séchées en
sortie de sécheur.
-
Transport des
boues séchées
C’est
une étape importante dans un atelier de séchage thermique car lors de ces
manutentions la structure granulée du produit peut être modifiée. Le transport
des boues séchées est souvent une source d’abrasion pour ces boues avec une augmentation
de la part de fines particules produites.
Il
existe différents types de convoyage des boues séchées :
·
La
vis convoyeuse,
·
Les
transporteurs tubulaires, à chaîne,
·
Les
transporteurs pneumatiques à phase dense ou à phase diluée,
·
Les
bandes transporteuses,
·
Les
élévateurs à godets.
Pour
le transport des boues séchées, il convient de tenir compte du degré de
séchage, en particulier de la taille des granulés et de leur température.
Dans
une boue totalement séchée (de l’ordre de 90% matières sèches), il peut y avoir
une production considérable de poussières en fonction du procédé de séchage.
Selon la nature du produit, des conteneurs fermés peuvent être nécessaires pour
le transport. La possibilité d'une explosion en raison de la création
d'atmosphères explosives lors du stockage ou du transport doit être étudiée.
Une gestion soignée de l'atelier doit permettre d'éviter des conditions
d'exploitation dangereuses.
Les
problèmes de corrosion et d'abrasion dans les silos et sur les appareils de
transport sont à résoudre par le choix de matériaux appropriés tels que l'acier
inoxydable, la céramique à l’intérieur des coudes lors d’un transport
pneumatique, etc.
Il
est important de signaler que le transport pneumatique des boues séchées modifie
très significativement la répartition de la granulométrie des boues séchées,
créant plus de fines particules. Ce point est notamment à prendre en compte
pour l’exutoire final des boues séchées (exemple : épandage).
Si
des filtres à manches sont utilisés pour la séparation des poussières, un
refroidissement en dessous du point de rosée est à éviter pour que les filtres
ne s'encrassent pas prématurément. Si ceci ne peut pas être évité, un chauffage
d'appoint peut être installé. En cas d'utilisation d'échangeurs thermiques pour
la condensation des buées, on doit envisager la séparation préalable des
poussières afin d'éviter l'apparition de dépôts et d'incrustations.
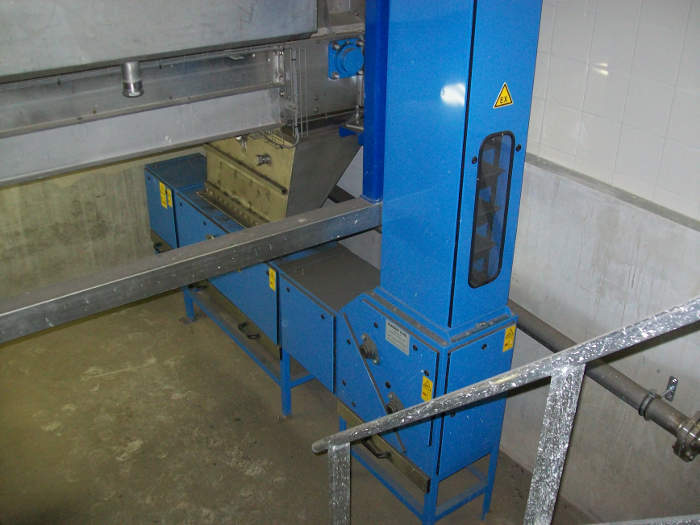
Elévateur à godets en sortie de sécheur
Optionnel =
mise en forme des boues séchées via la pelletisation :
Certaines
technologies de sécheur nécessitent, en aval, une mise en forme des boues
produites car ces sécheurs produisent un produit final insuffisamment granulé. Grâce
à un équipement spécifique nommé pelletiseur, il est ainsi possible d’obtenir
des boues séchées pelletisées, très calibrées, et ayant une très bonne densité.
Cependant,
il est important de souligner que les pelletiseurs et leurs équipements
associés (trémie tampon, mélangeur, refroidisseur à l’air, et filtre à manches
sur l’air du refroidisseur) sont difficiles à exploiter et entrainent des coûts
d’exploitation élevés. En effet, les pelletiseurs souffrent d’une usure
importante des pales occasionnant des renouvellements fréquents et surtout une
diminution importante de la disponibilité de l’atelier de séchage. En plus de
la mise en place d’équipements ATEX, les pelletiseurs sont très sensibles aux
variations de qualité de boue qui entrainent des arrêts non programmés très
importants, réduisant encore plus la disponibilité de l’atelier de séchage.
Le
retour d’expérience des exploitants concernant cet équipement est négatif. Si
la mise en place d’une unité de pelletisation peut être évitée dès la conception,
l’exploitation globale de l’atelier de séchage thermique n’en sera que
facilitée.
-
Stockage des
boues séchées
En
fonction de la destination finale des boues séchées, celles-ci peuvent être
stockées dans différents types de stockage :
-
Stockage courte durée en silo,
-
Stockage courte durée en benne,
-
Stockage longue durée en casier,
-
Stockage longue durée en vrac,
-
Stockage longue durée en big-bags.
Quel
que soit le type de stockage choisi, la température des boues en entrée de
stockeur doit toujours être inférieure à 40°C, voire 35°C si les boues
présentent des risques élevés, afin de limiter les risques liés à la
problématique d'auto-échauffement des boues.
Les silos sont, en
général, cylindriques. L’ensemble est monté sur des pieds de hauteur suffisante
pour permettre aux camions, et notamment aux citernes spécifiques au transport
des matières dangereuses de passer (se reporter au paragraphe « Evacuation
des boues séchées »). Cette hauteur est donc au minimum de 4,70 m, et
idéalement de 6 m afin que la rambarde de sécurité située sur les citernes ADR
(european Agreement concerning the
international carriage of Dangerous
goods by Road, accord européen
relatif au transport international des marchandises dangereuses par route)
puisse être déployée. Le silo et ses accessoires doivent être réalisés selon
les codes et normes applicables pour ce type de matériel, notamment en ce qui
concerne la prévention des risques d’explosion (guirlandes de températures,
double capteur de CO dans le ciel gazeux, inertage à l’azote, évents
d’explosion,…).
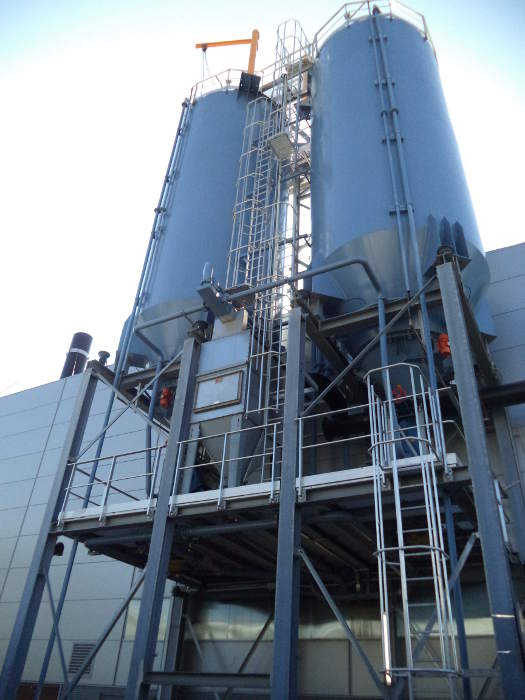
Silos de stockage des boues séchées
Le stockage en
casier
permet de stocker des boues séchées sur des périodes de quelques semaines à
plusieurs mois. Un grappin fixé sur un pont mobile permet d’étaler les pellets
ou les granulés de boues séchées. Le grappin est un équipement ATEX (ATmosphère
EXplosive).
Le stockage en
vrac
permet également de stocker des boues séchées sur des périodes de quelques
semaines à plusieurs mois. Ce type de stockage est déconseillé si les boues
séchées présentent des risques vis-à-vis de l’auto-échauffement. Il est parfois
mis en place sur des boues séchées identifiées les moins problématiques par
rapport au phénomène d’auto-échauffement : boues d’aération prolongée sans
déphosphatation tertiaire, sans décantation, et sans ajout de graisses
externes.
Le stockage en
big-bag
permet également de stocker les boues séchées de quelques semaines à plusieurs
mois. Il ne faut pas accoler les big-bags, mais les espacer d’une dizaine de
centimètres en largeur et en longueur. Il est déconseillé de stocker des
big-bags sur une hauteur supérieure à 3 big-bags, ceux-ci étant positionnés sur
des châssis métalliques spécifiquement conçus. Ce type de stockage est, malgré
un coût plus élevé en exploitation qu’un stockage en casiers (de par les
manipulations des différents big-bags), conseillé lorsque la boue séchée est
réactive à très réactive thermiquement car les calories produites par
l'auto-échauffement sont facilement évacuées.
-
Evacuation des
boues séchées
La
réglementation du transport routier des matières dangereuses permet de mettre
en œuvre les mêmes essais (tests définis par l’ONU) pour la classification du
transport des matières dangereuses et pour l’étiquetage des produits
Le
test ONU N4 (catégorie des solides auto-échauffant) est à réaliser sur un
échantillon de boue séchée produite afin de caractériser le caractère auto-échauffant
ou non d’une boue.
Si
le test ONU N4 est positif, la boue est considérée comme auto-échauffante. L’évacuation
des boues séchées doit alors être réalisée par des citernes ADR. Dans ce cas,
il n’est plus possible de les évacuer via des bennes classiques Ampliroll.
.jpg)
Si
par contre le test ONU N4 est négatif, la boue est considérée comme non
auto-échauffante et elle peut être évacuée du site avec des bennes classiques.
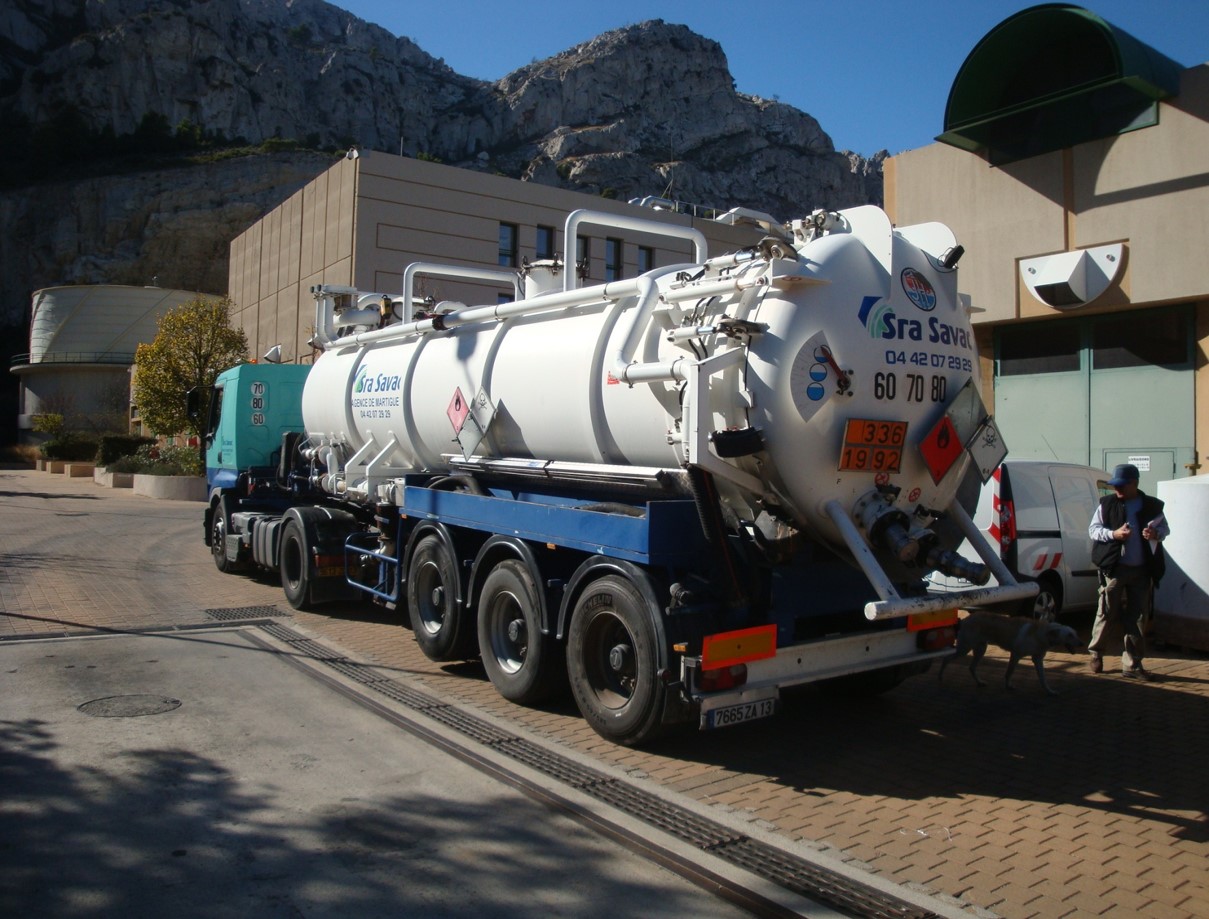
Citerne ADR pour le transport des boues séchées.
Les équipements communs
dans un atelier de séchage thermique
-
Ventilation de
l’atelier de séchage :
La
ventilation d’un atelier de séchage thermique est un élément clé lors du
dimensionnement, ainsi que lors de l’exploitation. L’atelier de séchage doit
être suffisamment ventilé afin d’évacuer les calories produites par le sécheur,
la chaudière, et les canalisations. La ventilation permet également de limiter
les odeurs dans certaines zones à risque de l’atelier telles que la sortie
liquide en pied de colonne de condensation, les zones ouvertes, …
Une
bonne surveillance du système de ventilation installé permet de garantir un
environnement de travail sain, aussi bien pour les opérateurs que pour les équipements.
- Utilités
Azote
Différents
équipements peuvent consommer de l’azote : les silos de stockage de boues
séchées (azote utilisé en secours pour stopper les montées en température dans
les silos) et le vase d'expansion si de l’huile thermique est utilisée comme
fluide caloporteur dans une chaudière. Ces équipements peuvent consommer de
l’azote en quantité différente, il faut donc veiller à ne pas sous-dimensionner
le stockage de l’azote pour les besoins.
Il
est conseillé de prévoir des débitmètres sur la canalisation d’azote afin de
connaitre la consommation d’azote en cas d’inertage d’un ou de plusieurs silos,
ainsi que pour connaître la quantité d’azote restant disponible.
Air comprimé
L’air
comprimé est un fluide notamment utilisé pour l’instrumentation mise en place
sur le sécheur. Une production d'air comprimé centralisée et correctement
asséchée pour le sécheur et ses périphériques avec des points d'utilisation à
chaque étage est la configuration à privilégier.
Eau industrielle
L’eau
industrielle peut avoir plusieurs utilités : refroidissement de certains
équipements thermiques, condensation, nettoyage des équipements … Il est donc
important de prévoir des points d'eau de nettoyage à chaque étage et notamment
dans les zones identifiées comme salissantes.
Eau potable
Un
réseau d’eau potable dans l'atelier de séchage est mis en place avec des points
à chaque étage et/ou point d'utilisation pour les besoins de nettoyage
effectués par les opérateurs.
Graissage
Lorsque
l’atelier de séchage est conséquent (notamment plusieurs lignes de séchage
et/ou de nombreux équipements périphériques), il peut être intéressant de centraliser
les points de graissage et d’envisager un graissage automatique.
-
Armoires
électriques, supervision, alarmes
Dans
la mesure où les ateliers de séchage thermique comportent des zones pouvant
être plus chaudes, plus humides ou plus poussiéreuses, il est recommandé de privilégier
le rapatriement des armoires électriques dans le local où se trouve le TGBT
(Tableau Général Basse Tension), et d’éviter les armoires dans les ateliers de
séchage. Si possible, des postes déportés de commande sont rajoutés dans
l'atelier.
Les
exploitants expriment également le souhait d’afficher les grafcets associés au
fonctionnement des équipements. Toutes les étapes et transitions des grafcets
ou langage SFC (langage graphique pour décrire les opérations séquentielles) sont
commentées, tous les bits et mots utilisés sont commentés, en règle générale,
toutes les possibilités de commentaires offertes par le logiciel de
programmation doivent être utilisées.
Plus
les équipements périphériques permettent de faire des bilans, via des
sous-compteurs par exemple (nombre d’heures de fonctionnement, consommation
électrique, …), plus la réalisation des bilans est facilitée pour les
exploitants.
Il
existe de nombreuses alarmes permettant aux exploitants de suivre, surveiller
leur installation. Il est nécessaire de déterminer les alarmes critiques et une
priorisation des alarmes est à mettre en place sur les ateliers de séchage
thermique (par exemple incendie, CO, O2, …).
Quelques considérations
relatives à la sécurité
Les
phases identifiées comme les plus à risques pour les équipements thermiques et
donc pour les ateliers de séchage thermique de boues urbaines sont les phases
d’arrêt et de démarrage. Les ateliers doivent donc être équipés de différents
capteurs (CO, CH4, H2S, voire NH3) placés à
des endroits appropriés de l’installation. Ces capteurs sont régulièrement
surveillés et vérifiés. Il convient de respecter des procédures détaillées de
démarrage et d'arrêt. Même après un arrêt prolongé, il existe un certain risque
d'explosion dû à la combustion lente de la boue qui est restée dans des zones
stagnantes. II convient que la combustion lente soit évitée par des procédures
appropriées telles qu'une stabilisation par l'addition d'eau ou de boue fraîche.
Les endroits particulièrement sensibles sont ceux à l'intérieur du sécheur, du
filtre à manche, … dans lesquels des matières sèches peuvent s'accumuler. Dans
les phases transitoires (démarrage/arrêt), l’oxygène est plus difficile à
contrôler ; ces matières stockées qui montent en température, peuvent
rapidement s’enflammer.
Dans
le cas des sécheurs à haute température de type direct, des préconisations de
sécurité particulières doivent être mises en œuvre. Il faut dans ce cas,
maintenir à un bas niveau la teneur en oxygène dans le sécheur proprement dit. On
prend en général une marge de sécurité de 2% par rapport à la CLO
(Concentration Limite en Oxygène), concentration à partir de laquelle un risque
d’incendie est possible. II peut être nécessaire d'augmenter cette marge de
sécurité, par exemple si la réponse des capteurs d'oxygène est lente ou si la
tête du détecteur est éloignée de l'endroit où la teneur en oxygène commence à
s'élever. Lors du choix d'un système de capteurs d'oxygène, il est important
que le fabricant confirme que ces capteurs peuvent être utilisés à une
température et une humidité élevées et lorsque des contaminants probables sont
présents. Des sécheurs à basse température de fonctionnement comme les sécheurs
à bande Evaporis™ LT ainsi que les sécheurs mixtes Evaporis™ LE n’ont pas ces
contraintes de sécurité.
La
surveillance de la température de nombreuses parties de l'installation est
également essentielle. La boue sèche est refroidie à la sortie du sécheur à une
température inférieure à 40°C et cette température est surveillée soigneusement
dans tous les circuits de transport et dans les silos de stockage. Tous ces
circuits sont maintenus sous une pression négative par un système de
ventilation qui permet de recueillir les poussières dans un filtre à manches et
un silo. II est prudent d'éviter de les ouvrir, en particulier après un arrêt
d'urgence. Bien entendu, la poussière doit être aspirée avant que le personnel
pénètre dans les circuits pour des travaux d'entretien ou de maintenance.
Enfin,
il est recommandé aux opérateurs de garder propre l'installation et d'éviter
les accumulations de poussière, surtout dans des zones telles que les machines
à fabriquer les granulés, les broyeurs et les tamis. Durant leurs rondes
d'inspection, il convient que les opérateurs vérifient également qu'aucune
étincelle ne soit émise par des bandes transporteuses usées ou par des paliers.
II convient qu'il n'y ait pas d'augmentation anormale de température due à la
friction.
L’alimentation
thermique du sécheur
Il
existe différentes possibilités d’apporter l’énergie thermique nécessaire à un
sécheur : une chaudière (au fuel, au gaz naturel, au biogaz, mixte gaz
naturel/biogaz, ou biomasse), une cogénération, des panneaux solaires
produisant de l’eau chaude, des échangeurs récupérant de l’énergie sur un
circuit de fumées à haute température, …
A
l’heure actuelle, les sources d’énergie thermiques les plus fréquemment
rencontrées sur des sécheurs thermiques en France sont les chaudières au gaz
naturel et les chaudières mixtes.
Quel
que soit le type de chaudière mis en place, il est important de prévoir des
débitmètres sur les canalisations de fluides qui seront utilisées. Au minimum,
des compteurs totalisateurs seront installés (1 compteur par brûleur). Ces équipements
permettent à l’exploitant de réaliser des bilans de consommation de l’atelier
de séchage.
-
Chaudières au
gaz naturel :
Les
principales recommandations sur les chaudières au gaz naturel sont :
·
Pour
les détendeurs de pression, privilégier si possible la solution détendeur
mécanique plus fiable et qui nécessite moins de maintenance que les vannes de
régulation,
·
Prévoir
un exutoire suffisamment important pour la purge de la chaudière et un petit
avaloir pour récupérer les jus de nettoyage,
·
Prévoir
également l'installation d'une bride à la sortie de la canalisation des fumées
pour pouvoir vider correctement le corps de la chaudière.
-
Chaudières
mixtes gaz naturel et biogaz
Les
principales recommandations sur les chaudières mixtes gaz naturel et biogaz
sont :
· Installer
un diamètre nominal de la canalisation de biogaz plus important que celui du
gaz naturel (car PCI biogaz < PCI gaz naturel),
· Faire
arriver les canalisations de gaz naturel et de biogaz perpendiculairement sur
le brûleur,
· Mettre
en place un calorifugeage de la conduite de biogaz afin de limiter la présence
d'eau condensée,
· Installer
un pot de purge ou dévésiculeur (système anti-gouttelettes) sur le biogaz et un
détendeur sur la canalisation de gaz et celle du biogaz,
· Privilégier
un basculement en automatique des chaudières du gaz de ville au biogaz et vice
versa,
· Ne
pas oublier de doubler les vannes de coupures automatiques (obligation
sécurité) sur les arrivées de gaz et biogaz,
· Laisser
accessible la vanne manuelle d'arrêt d'urgence de la chaudière (à localiser à
l'extérieur du bâtiment pour être accessible par les pompiers en cas de besoin).
-
Panoplie gaz sur
les brûleurs
Les
bonnes pratiques et les erreurs à éviter en matière de panoplie gaz sur les
brûleurs sont :
· Prévoir
des panoplies séparées sur chaque brûleur et chaque combustible,
· Privilégier
les postes de détente mécanique,
· Instrumenter
chaque ligne gaz séparément pour pouvoir effectuer des bilans par brûleur. Il
existe des compteurs gaz permettant d’afficher directement la consommation de
gaz corrigée en Nm3/h. En cas de compteur volumétrique en m3/h,
le rajout d’un pressostat permettra de pouvoir ensuite faire la conversion par
le calcul,
· Eviter
de réguler la pression sur une ligne avec plusieurs brûleurs,
· Eviter
les vannes de régulation de pression,
· Il
faut une indépendance des lignes d’alimentation en combustible : une ligne
distincte par type de combustible, ainsi qu’un brûleur, pouvant être
multi-combustible, par chaudière sinon les fluctuations d’un brûleur impactent
les autres
Disponibilité de
l’atelier de séchage
Le
dimensionnement d’un sécheur thermique est souvent réalisé sur une base de 7 500
h/an. Il est fortement recommandé d’envisager l’exploitation d’un atelier de
séchage sur un mode de fonctionnement continu, au minimum sur une période de
plusieurs jours consécutifs. En fonction du mode d’exploitation de la station
(quarts, astreinte la nuit, présence de personnel le week-end, …), cette durée
de fonctionnement peut être abaissée. Il est important de signaler que le fonctionnement
de l’atelier de séchage dépend certes du sécheur en lui-même, mais également des
équipements périphériques : plus les équipements périphériques sont
nombreux, en particulier en cas de pelletisation, plus la disponibilité globale
de l’atelier de séchage va diminuer. Il ressort des bilans d’activités réalisés
en France qu’il est difficile de faire fonctionner un atelier de séchage plus
de 6000 h/an.
En
effet, les phases de maintenance (préventives et curatives) deviennent de plus
en plus nombreuses avec l’augmentation du nombre d’équipements. Il convient de
ne pas sous-estimer les besoins en personnel pour la conduite de telles
installations. Il ne faut pas oublier qu’il s’agit d’équipements thermiques
avec des risques spécifiques identifiés tels que les fluides chauds (huile
thermique ou vapeur) et donc des risques de brûlures, des machines tournantes,
des équipements électriques, … Par ailleurs, un niveau de formation élevé est
exigé pour tous les nouveaux opérateurs et chefs d'équipe (formation théorique
mais également pratique : exploitation, maintenance, et situations
d'urgence).
Conclusion et
perspectives
Un
soin particulier doit être apporté aux équipements périphériques d’un sécheur
thermique, tant au stade de la conception que lors de la construction afin de
faciliter les conditions d’opération et de maintenance pour les exploitants.
Le
séchage thermique des boues est une solution qui permet d’élargir le champ des
modes d’évacuation ou de valorisation des boues. Les boues séchées à 90%MS présentant
un bon pouvoir calorifique inférieur, les filières thermiques d’incinération et
de co-incinération peuvent notamment être une bonne solution finale pour
valoriser ces boues séchées. Les boues séchées sont en France majoritairement
valorisées en agriculture (épandage ou compostage) : l’aspect des boues
séchées, la teneur agronomique des boues séchées ainsi que l’hygiénisation et
la stabilisation sont fortement appréciés.
Les
retours d’expérience, riches et variés, capitalisés par le GEST vont contribuer
à l’évolution de la technologie de séchage avec pour objectifs, la réduction de
la consommation thermique, l’amélioration de la fiabilité des unités et de leur
taux de disponibilité, ainsi que le renforcement des connaissances sur le
comportement des boues séchées.