Les solutions ne manquent pas pour séparer et traiter les graisses présentes dans les eaux usées industrielles. L’enjeu aujourd’hui est de réduire le coût de ces opérations, avec deux options : miser sur l’économie circulaire ou sur l’ergonomie des appareils.
.jpg)
Quinze ans se sont écoulés depuis que les graisses collectées dans les eaux usées ont été bannies des centres d’enfouissement des déchets. Les stations d’épuration ne les acceptent plus qu’à faibles doses. Les industriels concernés par l’élimination de telles matières ont donc dû s’équiper pour traiter leurs effluents en amont. Mais cela génère des coûts que les entreprises cherchent aujourd’hui à limiter. Certaines, dans l’agroalimentaire notamment, ont pris conscience que les graisses ont un fort pouvoir calorifique. Plutôt que de payer pour évacuer leurs boues graisseuses vers une filière de destruction classique (incinérateur, etc.), elles les mettent à la disposition de sites de méthanisation. Les plus grosses se dotent mêmes de leur propre unité.
.jpg)
Méthaniser pour valoriser
Les graisses sont difficiles à méthaniser seules. Leur complexité chimique les rend peu digestes. Mais, mélangées à d’autres déchets organiques, elles optimisent la fermentation anaérobie, donc la production de biogaz. Une aubaine pour les fabricants de plats cuisinés par exemple, qui peuvent ainsi valoriser leurs multiples sous-produits alimentaires. Ou encore pour le site du groupe Danone à Tchekhov (Russie) : « avant, les boues graisseuses physico-chimiques y étaient traitées à l’extérieur, à un coût très élevé. Quand l’usine nous a sollicités pour améliorer sa station d’épuration, nous avons proposé de l’équiper d’un méthaniseur de 2.000 m³, capable de digérer 29.000 tonnes de boues graisseuses par an, explique Antoine Lemaire, directeur général délégué chez CMI Proserpol. Le biogaz émis - représentant 30.000 kWh de pouvoir calorifique inférieur (PCI) - est utilisé directement dans la chaudière du site ». Au final, la rentabilité du traitement s’en est trouvée améliorée, tout comme les consommations d’énergie et de déchets.
Mais la méthanisation directe des graisses pures est délicate à mettre en œuvre.
Les matières grasses pures sont insolubles, moins denses que l’eau, le plus souvent lentement biodégradables et certains acides gras sont suspectés d’être inhibiteurs d’une partie des micro-organismes méthanogènes.
Or, certaines industries agroalimentaires, comme les laiteries ou les producteurs d’huiles végétales, ne génèrent pas d’autres déchets organiques avec lesquels mélanger leurs graisses. « Pour ces sites, nous avons réussi à contourner le problème, annonce Hans Van Soest, dirigeant d’Enprotech. Nous avons mis au point un nouveau réacteur, l’Enprotech OptiActor, dans lequel les graisses sont liquéfiées, avant d’être envoyées dans un réacteur anaérobie capable de les traiter en même temps que le reste des eaux usées ». La première installation de ce type vient d’être mise en service dans une grande laiterie de Pologne ; une autre devrait bientôt voir le jour en France. Comment fonctionnent-elles ? Les graisses sont séparées puis placées quelques jours dans un bassin, le temps qu’elles se liquéfient naturellement, par hydrolyse. Elles sont ensuite réinjectées dans le circuit des eaux usées, après que celles-ci aient été prétraitées. L’ensemble passe dans un réacteur anaérobie, l’Enprotech Anaerobic BioActor, qui digère les matières organiques liquides, puis par un réacteur aérobie classique, qui parfait l’épuration. Au final, 98 à 99 % de la demande chimique en oxygène (DCO), donc des graisses, ont disparu. « Si notre solution représente un coût, le retour sur investissement est très rapide, affirme Hans Van Soest. Prenons l’exemple d’une usine qui envisagerait d’augmenter sa production. En ajoutant à son réacteur aérobie notre solution (hydrolyse et traitement anaérobie), les frais d’exploitation après extension seront moins élevés qu’avant, même si la quantité de graisses générée est plus importante. En effet, il ne sera plus nécessaire d’évacuer les graisses et le site bénéficiera de leur valorisation énergique ».
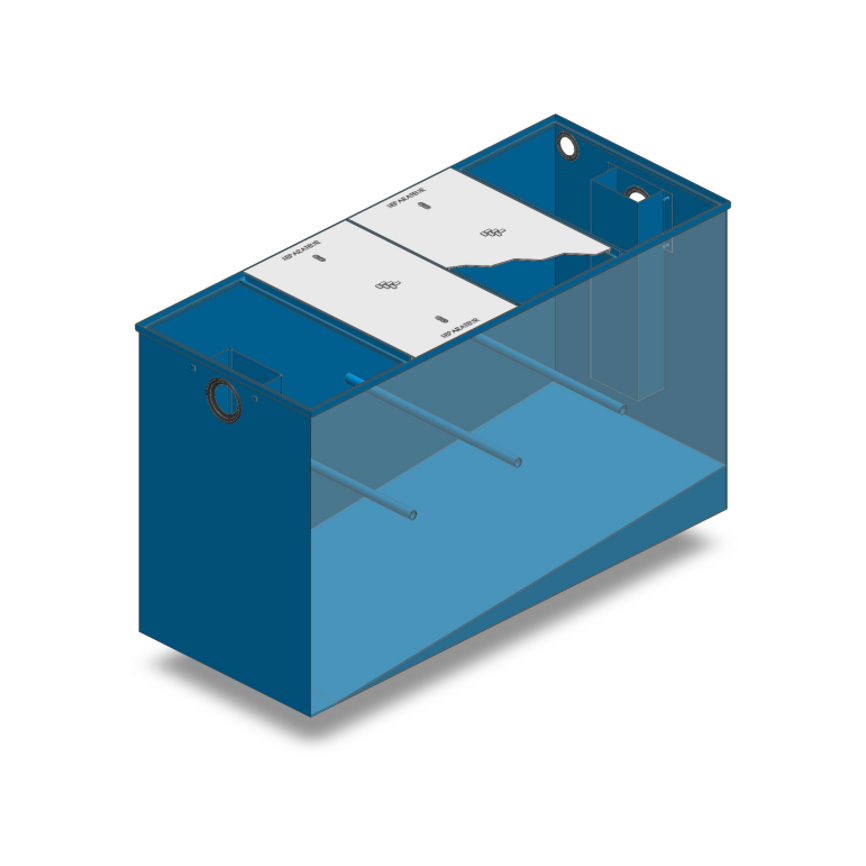
Les usines de taille plus modestes auront sans doute intérêt à s’insérer dans un écosystème circulaire, en mettant leurs graisses à la disposition de méthaniseurs. Mais il leur faut préalablement bien les séparer. Un prétraitement qui nécessite de recourir à de différents équipements tels que bacs à graisse, débourbeurs, séparateurs, presses à disques, filtres à bandes, centrifugeuses… etc, développés par R & O Dépollution, EMO, KWI, Purostar, Saint Dizier Environnement, Simop, Vogelsang ou encore Atlantique Industrie. « Pour les sites comme par exemple les abattoirs dont les eaux usées contiennent des morceaux de graisses, nous proposons un séparateur à disques qui, de par sa conception (avec une rotation continue opposée des grilles de filtration), s’auto-nettoie en permanence, ce qui lui permet de conserver une capacité de traitement stable », explique Jean-François Gautreau, chargé d’affaires chez Atlantique Industrie.
Les eaux filtrées peuvent poursuivre leur parcours vers un bassin de flottation.
.jpg)
Reste la question du transport des graisses vers le méthaniseur, qui conditionne l’intérêt de tels projets « Un bilan thermique entre le biométhane produit par les apports complémentaires de graisses sur le méthaniseur et les calories dépensées pour préchauffer les graisses s’impose, comme le conseille un contributeur sur le forum d’entraide technique FluksAqua. Si ce bilan est positif, différentes solutions permettent de transporter les graisses sur des distances importantes en les maintenant à une “température supérieure à 15° pour éviter qu’elles ne se figent dans les canalisations ». Il mentionne par exemple la mise en place d’une boucle de biométhane en retour du méthaniseur vers la station d’épuration pour préchauffer les graisses dans leur cuve de stockage via une chaudière gaz. Un autre exploitant actif sur le forum propose la mise en place d’un « double réseau enterré (protection naturelle contre le gel) avec une ou deux (sécurité) pompes à pistons dites pompes à béton, du type Putzmeister par exemple ». Matériel qu’il juge « parfaitement adapté à ce type de produit ». Il ajoute qu’avec une production lissée, des canalisations haute pression, un maximum de longueur droite et des coudes grand rayon, le tout bien maintenu (prévoir des regards au niveau des accouplements des canalisations, partie la plus fragile), le transport de la graisse peut se faire de manière optimale. Les pompes à piston (Putzmeister, Schwing, Serip ou Abel) sont recommandées par plusieurs exploitants du forum dans ce type de configuration.
.jpg)
Le stockage des graisses doit lui aussi être étudié dans ce type de projets : pour éviter qu’elles ne figent dans les cuves de stockage, plusieurs options sont envisageables selon les professionnels de l’assainissement qui en débattent sur le forum FluksAqua : liquéfaction par injection de soude à 30 % à un pH de 12 sous agitation, ou par un serpentin d’eau chaude alimenté par l’énergie sur site. « La mise en place d’un broyeur à couteaux et de pompes à lobe (Börger, Vogelsang…) assurera ensuite une recirculation par canardage », explique un contributeur.
Travailler les design pour optimiser la flottation
Les aéro-flottateurs permettent d’améliorer l’efficacité du prétraitement des graisses, notamment lorsque les bassins tampons ne sont pas en capacité de les refroidir (graisses à trop haute température, séparateur à graisse sous-dimensionné…). C’est l’expérience que partage sur le forum Fluksaqua un exploitant de deux stations de prétraitement chez des industriels dans agroalimentaire, dont l’un produit exclusivement du canard, avec des concentrations en graisses très élevées et une température supérieure à 35°. « Même un grand bassin tampon (60 m³) ne permet pas de refroidir suffisamment l’effluent pour figer les graisses afin de les bloquer dans un tamis rotatif à maille fine, explique-t-il. Seule une flottation à air dissout permettrait d’atteindre des rendements suffisants pour ne pas perturber le traitement de l’unité ».
.jpg)
Les graisses liquides remontent naturellement à la surface des eaux. C’est sur ce principe que repose la flottation. Un mécanisme que les constructeurs optimisent en injectant de l’eau pressurisée dans les circuits : les microgouttelettes de graisses sont ainsi “piégées” par de très fines bulles d’air qui les conduisent plus vite vers le haut, où elles sont raclées avec l’écume. Souvent, pour collecter jusqu’aux nanoparticules dispersées dans les effluents bruts, le processus est complété par l’ajout de réactifs : des coagulants et des floculants qui favorisent l’agglomération de ces nanoparticules sous forme de flocs. Mais, quand le digestat de la méthanisation a vocation à être utilisé en épandage, mieux vaut éviter le recours à de tels produits. Certains comme Aquadep, Serinol, Biotec Environnement, TecBio ou Hydranet ont donc perfectionné leurs équipements. KWI France, par exemple, peut proposer de mettre en série deux de ses flottateurs Unicell™ pour atteindre un meilleur taux de dégraissage, et ainsi respecter les normes de rejet sans ajout de réactif.
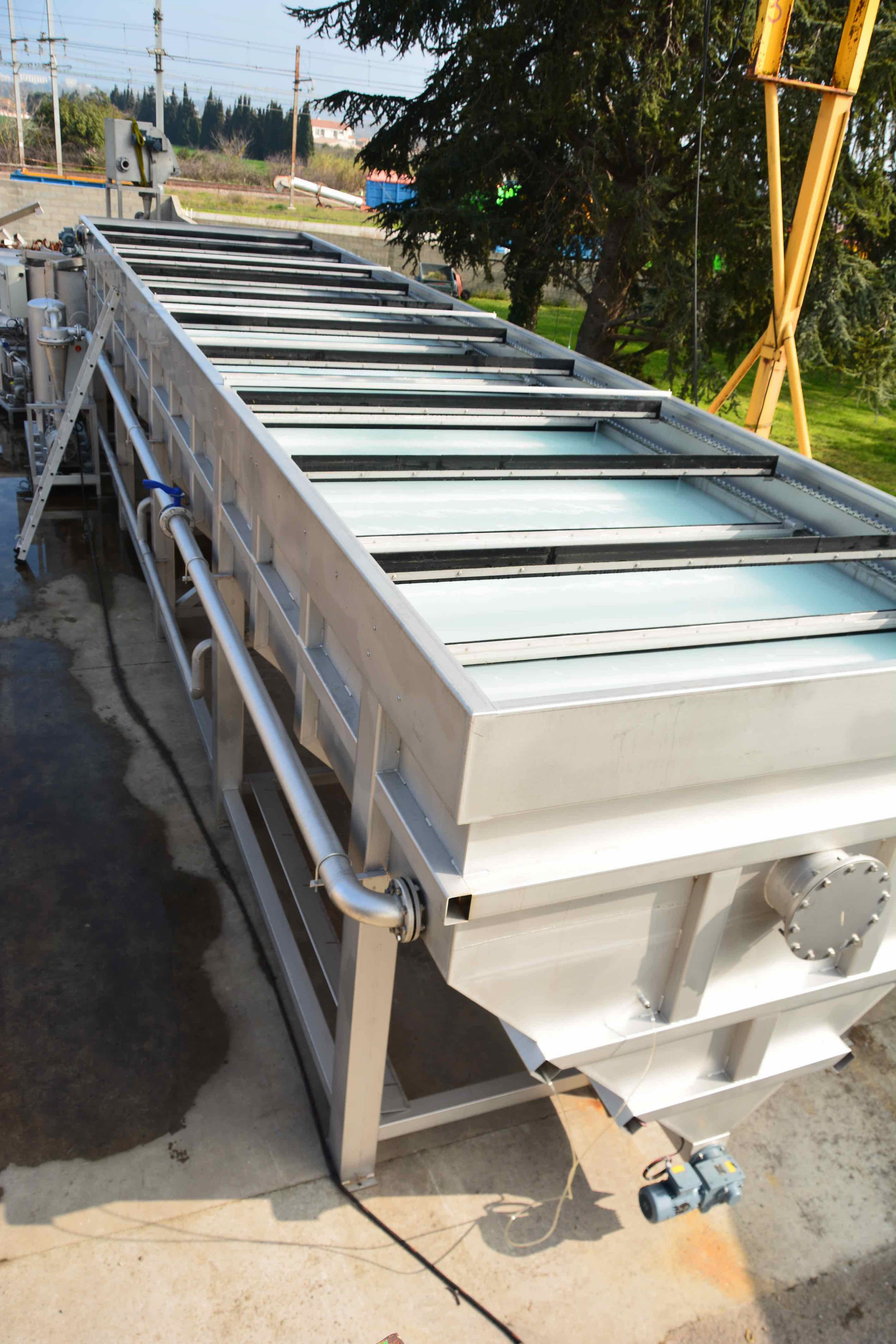
D’autres améliorent le design de leurs cuves pour réduire les coûts d’exploitation. « La facilité d’utilisation est aussi importante que l’efficacité. Un matériel aisé à exploiter, qui demande le minimum d’intervention humaine, a plus de chance de fonctionner correctement et coûte moins cher en maintenance, indique Gregory Reynaud, directeur de Purostar. C’est ce que nous avons cherché à obtenir avec notre flottateur. Celui-ci se distingue par sa forme cylindrique et l’axe unique qui, en son centre, fait tourner en même temps un racleur de surface et un racleur de fond. L’un, en tournant dans le sens opposé au mouvement de circulation de l’eau, collecte plus efficacement la phase graisseuse ; l’autre aide à évacuer les matières décantées, ce qui limite l’encrassement du bassin ».
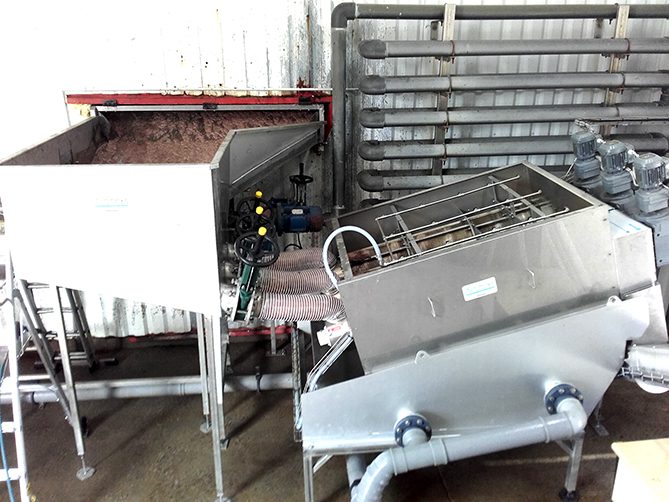
Atlantique Industrie mise de son côté sur une solution simple et rustique pour le traitement des graisses reposant sur un pressage de boues directement en sortie de flottateur. « Nous utilisons une presse à disque MDS derrière un flottateur air dissous, sans ajout de floculant, explique Jean-François Gautreau. Les graisses en sortie de flottateur sont à environ 10 % de matière sèche. Après pressage nous obtenons une siccité entre 35 et 40 % ». Ces résultats sont conditionnés par l’absence de manipulation de la boue entre le flotatteur et la presse pour éviter toute destruction du floc due au pompage, à la vis de transfert ou au brassage lors du stockage. Le gavage de la presse doit donc être gravitaire. Parmi les avantages du procédé, une faible consommation d’énergie (2,2 kW) en comparaison de systèmes traditionnels, une consommation de polymère nulle, une reprise des boues possible par vis benne ou godets (boues pelletables tenant en tas), une faible consommation d’eau et un coût de maintenance très bas.
Coagulants et floculants réduisent la charge
« L’injection de coagulants et de floculants permet un taux de dégraissage supérieur à 95 % », poursuit Gregory Reynaud. C’est ainsi que, dans les ateliers d’entretien des métros parisiens, dont les effluents sont chargées en huiles et graisses à hauteur de 1.000 mg/l, Purostar parvient à réduire la charge polluante des eaux à moins de 5 mg/l.
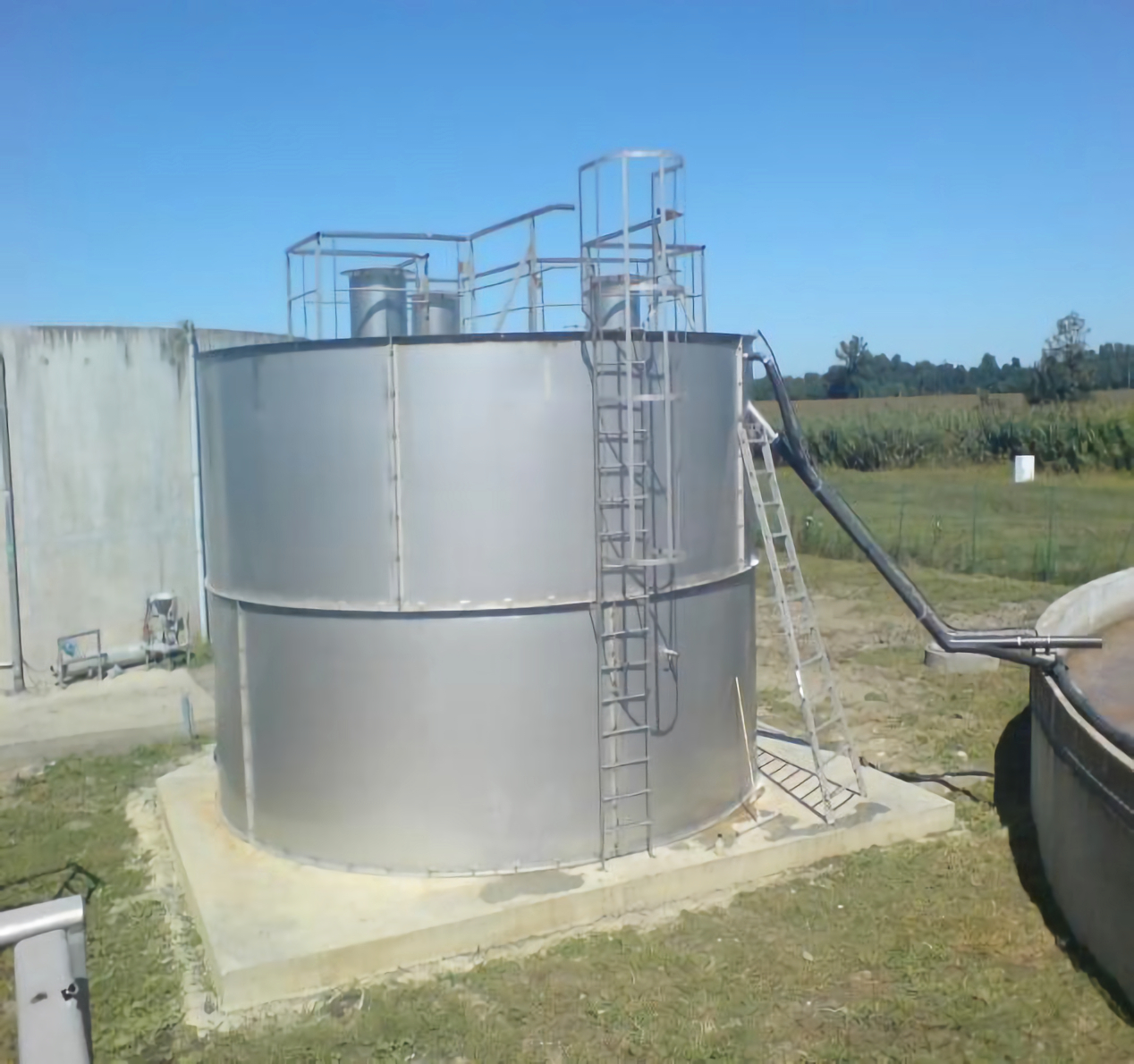
Pour Afig’eo, spécialiste du traitement des eaux usées dans l’aéronautique, l’automobile et l’horlogerie, « l’élimination des huiles mécaniques issues du nettoyage de pièces ne représente qu’un aspect de notre travail, qui se concentre sur les métaux lourds, explique Dominique Buzaré, directeur technique de l’entreprise. Réalisée en amont, cette opération limite néanmoins les risques de colmatage des sondes et tuyauteries. Parfois, il suffit de laisser décanter. Mais, le plus souvent, nous injectons un réactif, qui libère les huiles pour mieux les séparer avec un petit déshuileur mobile ou fixe. Le procédé que nous utilisons ensuite pour insolubiliser les métaux - l’électrocoagulation - fait le reste. Il s’agit de compartiments dans lesquels on applique un champ électrique. Quand l’effluent passe dedans, les métaux et les graisses sont co-précipitées par le courant. Nous récupérons alors le tout dans un filtre-presse. Cet effet secondaire de notre traitement ne fonctionne cependant qu’avec une quantité limitée de graisse ».
Les traitements aérobies conservent leur place
Plus économiques qu’un envoi en incinération, les traitements aérobies ont toujours leur place sur les eaux chargées en graisses. Le principe est simple : il s’agit de mettre les effluents en contact avec des bactéries sélectionnées naturellement, pour les transformer en biomasse assimilable par les stations communales.
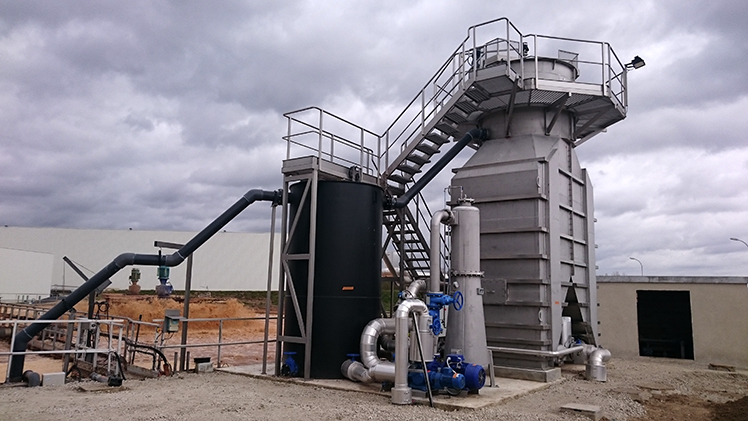
Ainsi, « le bioréacteur Carbofil®, que nous commercialisons depuis près de 20 ans, est utilisé en prétraitement dans de nombreuses stations d’épuration », rappelle Michel Delas, directeur commercial de RWL Water. Le procédé repose sur une forte oxygénation et un brassage intense, ce qui assure une biodégradation quasi-totale. Le bioréacteur se présente sous la forme d’une cuve en résine ou en béton à l’intérieur de laquelle une hélice propulse le liquide à traiter vers le fond. Puis le fluide remonte par les côtés et passe par-dessus une coupole, un mouvement qui entraîne de l’air et ravale en continu la mousse. Pendant tout le process, des bulles d’air sont envoyées au fond du réacteur. La pression qu’elles subissent pendant l’opération provoque une solubilisation maximale de l’oxygène, selon la loi de Henry.
Eurobio a développé de son côté un procédé pour les graisses et boues issues de coagulation/floculation qui vient d’être breveté au niveau européen. Il repose sur biodégradation aérobie des graisses par un biodigesteur adapté forte charge (jusqu’à 10 kg de MEH/m³/j) comportant un bioreacteur intégré cultivant des souches lipasiques sélectionnées. La mise en œuvre de ce bioréacteur évite l’installation d’un bassin d’hydrolyse dont on connaît les aspects négatifs. L’aération du biodigesteur est réalisée en permanence 24h sur 24 par une turbine (type roue à aube) qui propulse la liqueur mixte oxygénée sur les parois.
Chez KWI France, « le Biofloat®, qui associe un traitement biologique faible charge et haute concentration avec une double flottation (co-courant et contre-courant), permet de passer de 8 g/l de biomasse à moins de 30 mg/l, soit d’obtenir un taux de clarification de la biomasse de 99,7 %, explique Denis Richard, directeur général de l’entreprise. Cela autorise un rejet au milieu naturel ».
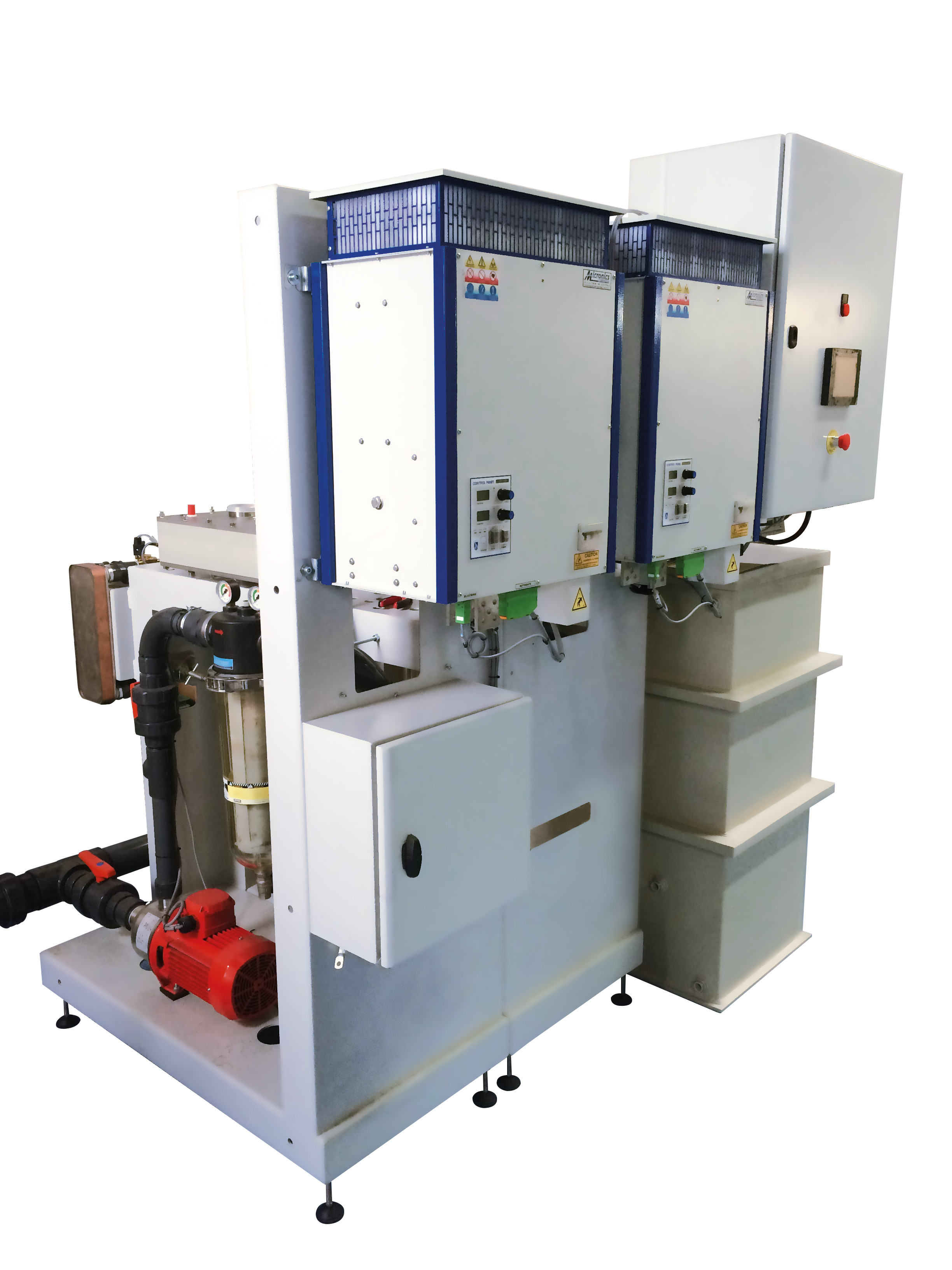
Le Biomaster™ de Suez est un autre procédé de dégradation biologique aérobie spécifique aux résidus graisseux sur des concentrations types de 50 à 300 g · L-1 de DCO des triglycérides. Les graisses à traiter sont mises en contact avec une biomasse épuratrice adaptée pour dégrader le substrat carboné qu’elles contiennent. La dégradation est matérialisée par une hydrolyse des graisses en acides gras et glycérol suivie d’une oxydation des acides gras en H2O et CO2.
Les performances sont atteintes avec un temps de séjour d’environ 3 semaines. De même, le procédé Agira™ de Veolia repose sur une cuve d’hydrolyse qui prétraite les matières grasses en présence de chaux avant qu’elles n’entrent dans un réacteur aérobie.
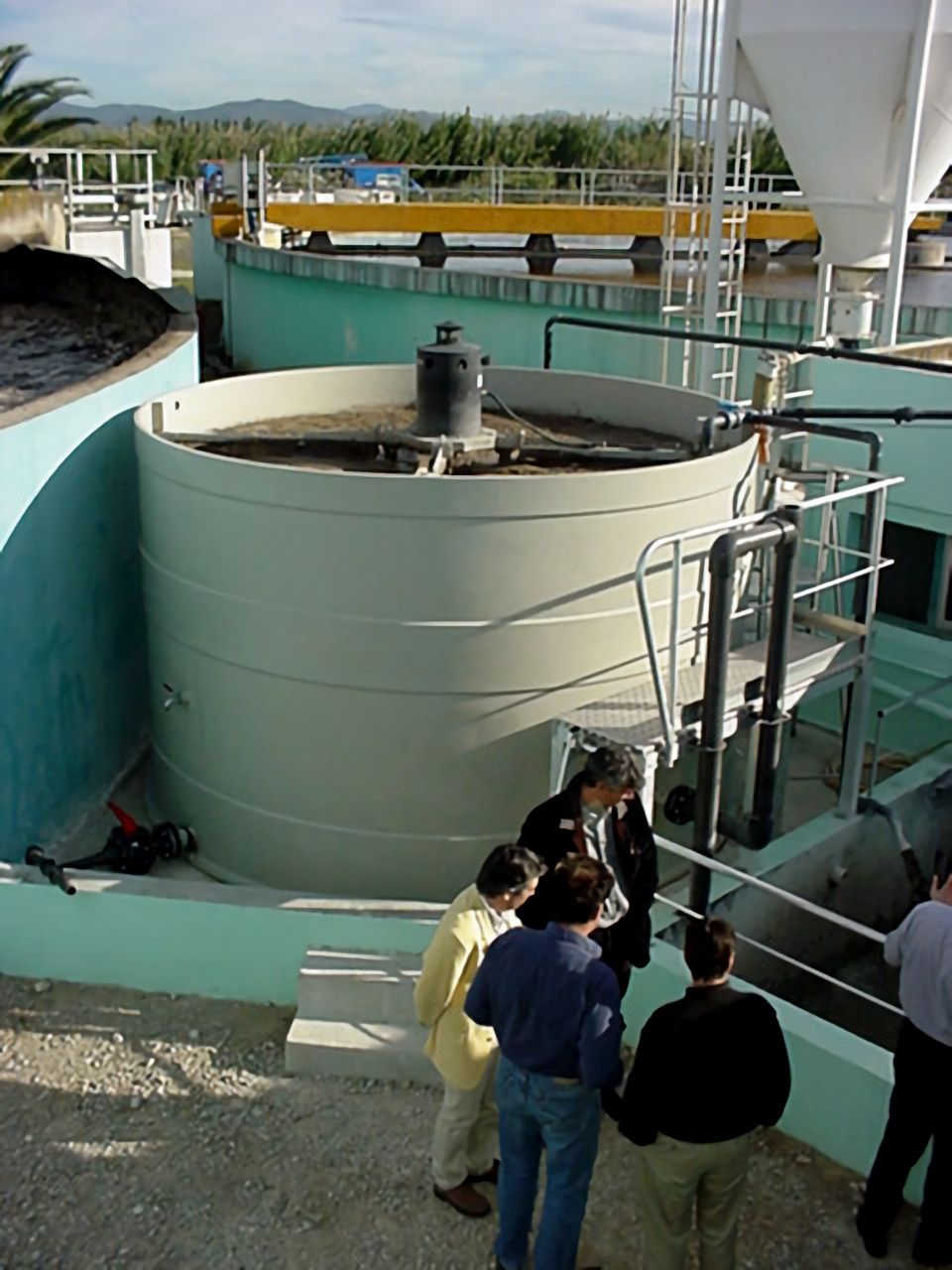
Chaque cas étant particulier (quantité et composition des effluents, normes de rejets à respecter, contraintes…), les constructeurs proposent presque toujours des solutions personnalisées.
Les process envisagés sont testés en laboratoire, voire in situ, ce qui permet de les valider mais aussi d’estimer au plus juste les coûts d’investissements et d’entretien à prévoir.
Élargir sans cesse la palette de traitements disponibles
Proposer de nouveaux types de traitement fait aussi partie des enjeux de la recherche.
Certains industriels développent de nouvelles technologies. C’est par exemple le cas de Waterdiam qui met en œuvre des électrodes en diamant artificiel pour traiter les eaux sans produit chimique. Les systèmes DiaClean® sont utilisés pour le traitement des eaux au sens large du terme et notamment pour le traitement d’effluents industriels en oxydant les molécules organiques, les huiles et les graisses grâce à la production de radicaux hydroxyles OH° sur le diamant, seul matériau capable d’atteindre de telles performances en électrolyse. De nombreux travaux menés en collaboration avec des universités et centres de recherche indiquent qu’aucune molécule organique ne résiste à cette oxydation. DiaClean® constitue un maillon manquant dans le recyclage et permet ainsi d’entrevoir de nouvelles possibilités de recyclage des eaux de procédés, afin de réduire la consommation d’eau propre et l’impact sur l’environnement.
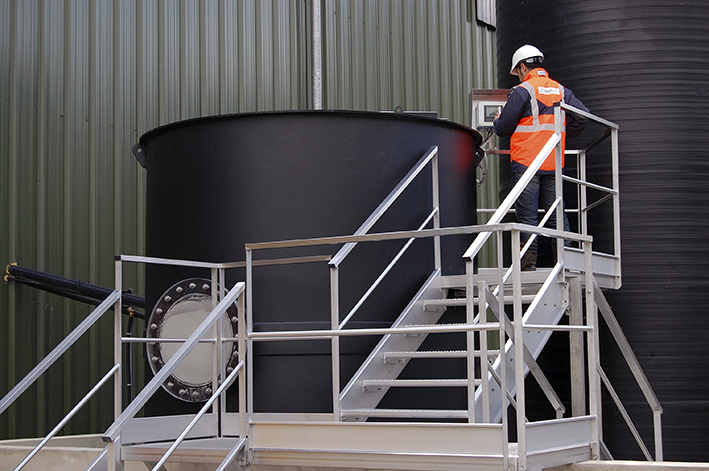
De même, Sapoval a développé une unité de prétraitement des graisses de flottation entièrement automatisée. Via un procédé exclusif de saponification, l’unité Sapo’Fix transforme ces graisses en un effluent liquide inodore qui peut être directement traité en circuit court par une station d’épuration ou un méthaniseur local. Une première unité a été mise en place chez Barnier Olives un agro-industriel héraultais.