Le traitement des effluents industriels, avant rejet, fait appel à des technologies parfois coûteuses. Or la pollution est en général concentrée dans une faible partie des effluents totaux d’une installation industrielle, d’où l’intérêt de séparer les flux pour ne traiter que le nécessaire. Reste à trouver les bons arguments pour convaincre les industriels de modifier, en profondeur, la gestion des flux au sein de leurs procédés.
.jpg)
D’où l’intérêt potentiel de séparer les différents flux pour les traiter chacun selon ses spécificités. Dans l’idéal, la séparation se fera dès le procédé industriel, ou, à défaut, en amont de la STEP. « Lorsque l’on s’intéresse à la valorisation des effluents industriels, il faut pouvoir analyser de manière pro-active le continuum unité de production station d’épuration en prenant du recul et progressivement localiser les sources de pollution, les économies possibles etc… Cette démarche n’est efficace qu’en analysant le procédé global depuis la réception des matières premières, des utilités jusqu’au point de rejet en sortie d’usine, explique Christophe Guillaumin, Chargé d’Affaires Séparation chez Alfa Laval, spécialiste dans la fourniture de solutions de séparation centrifuge et évapoconcentration. En effet, bien des effluents sont valorisables lorsqu’ils sont captés avant d’être mélangés et envoyés vers la station d’épuration. Nous sommes donc encore dans le procédé de fabrication, mais dans une zone grise, souvent peu considérée par l’industriel ».
Une connaissance fine des flux est requise
« La séparation des flux dès le procédé est surtout l’affaire des bureaux d’étude qui répondent aux appels d’offres des industriels, souligne de son côté Maxime Pollet, responsable commercial chez Ovive. Ils analysent et cartographient les flux. Nous, fournisseurs de solutions de retraitement, nous arrivons après ». Ce que confirme Antoine Lemaire, directeur général délégué de CMI Proserpol : « quand nous recevons un appel d’offres, la cartographie des flux et de la pollution est déjà faite. C’est le métier de bureaux d’études qui interviennent aussi pour les bilans de pollution, les autorisations d’exploiter, les études d’impact… L’industriel s’appuie sur leur travail pour s’adresser à l’administration, ou aux fournisseurs d’installations de retraitement ». Quelquefois, les grands groupes industriels possèdent même leur propre expertise quant à leurs effluents. Ce sont souvent les entreprises de taille plus modeste qui doivent faire appel aux bureaux d’étude.
.jpg)
« Faire appel à un bureau d'études comme Antea Group permet d’obtenir un conseil objectif, pragmatique et indépendant de tout fournisseur ou exploitant. Cela nous arrive de redéfinir un cahier des charges irréaliste, comme ce cas d'un dépôt de carburant qui nous avait sollicité pour traiter 1.200 m³/h d'effluent en mélange avec du pluvial ; nous avons recentré sur la problématique de la DCO sur quelques centaines de mètres cubes dus à des purges de bacs de stockage mal maîtrisées » précise Rémi Faucher.
Plusieurs traiteurs d’eau disposent en interne des compétences nécessaires pour s’investir dans un examen approfondi de tous les procédés susceptibles de générer des flux devant être traités. C’est par exemple le cas des grands tels que Veolia, Suez ou OTV DBI, mais aussi de Waterleau, Chemdoc Water ou encore Nereus.
.jpg)
Il arrive toutefois que les traiteurs d’eau aient leur mot à dire sur la gestion des flux. « Une de nos stations d’épuration, installée chez un industriel, souffrait d’un apport de zinc. Nous avons nous mêmes identifié dans ses chaînes l’unité envoyant le zinc et isolé ce flux, que traitons à part sur un petit procédé physico-chimique » explique par exemple Maxime Pollet. Serep, filiale de Veolia, a de même été amenée à “entrer” dans le procédé d’un client. « Sur une installation récente, nous avons adopté une démarche de partenariat avec un bureau d’étude. L’industriel rejetait 400 m³/jour d’effluents. Or, la cartographie nous a montré qu’un dixième seulement de ce volume était véritablement polluant. Nous avons donc conçu une installation spécifique pour ces 40 m³, le reste étant envoyé sur une station d’épuration classique » se souvient Stéphanie Rossignol, responsable commerciale du département Ingénierie Traitement des Eaux chez Serep.
Des réticences à lever
.jpg)
Isoler les flux les plus chargés ne signifie pas forcément traiter chaque type d'effluents séparément.« On peut agir sur un process générant des effluents, comme par exemple modifier un dispositif de pousses à l'eau dans les canalisations par des pousses à l'air et récupérer du produit fini » précise Rémi Faucher chez Antea Group.
.jpg)
Mais la principale réticence est d’ordre économique. Il faut prouver que l’investissement initial nécessaire pour séparer les flux est largement compensé par la suite en termes de coûts de retraitement des effluents. « En identifiant la source de pollution, on peut mettre en œuvre une technique ciblée et, du coup, prévoir des installations plus simples pour retraiter le reste. Ce n’est donc pas toujours plus cher, au contraire » plaide ainsi Stéphanie Rossignol chez Serep… tout en soulignant que si l’option de séparer les flux n’est pas prévue dès la conception du procédé, il sera difficile de convaincre l’industriel de réaliser d’importants travaux hydrauliques sur sa chaîne de production. « L’investissement est supérieur, c’est vrai, mais le client y gagne au final car la station d’épuration, en sortie de site, fonctionne beaucoup mieux, d’où un gain d’exploitation » confirme Maelle Willot.
.jpg)
« Pour convaincre l’industriel, nous lui présentons les deux scénarios : soit une grosse station d’épuration avec les coûts d’exploitation afférents, soit des flux isolés en amont et une petite STEP. Tout dépend des flux et des coûts d’externalisation. Certaines pollutions sont valorisables, d’autres évacuables à coût nul, d’autres peuvent coûter cher », explique pour sa part Maxime Pollet chez Ovive. L’industriel peut en effet avoir intérêt à récupérer certaines matières polluantes. « Nous avons réalisé une installation dans une usine pharmaceutique du Morbihan. Nous reconcentrons un flux riche en composés organo-iodés. Or l’iode coûte très cher. L’industriel récupère donc une valeur marchande sur une partie de son effluent » expose Maxime Pollet. Dans le même ordre d’idée, Serep est spécialiste de la séparation des hydrocarbures, qu’elle sait valoriser. Et dans l’agroalimentaire, il devient fréquent de proposer la séparation de tout ce qui est méthanisable.
L’agroalimentaire… et le reste
L’agroalimentaire représente un cas extrême, avec ses flux riches en graisse ou en sucres, dont les pics peuvent déstabiliser une station de traitement aérobie, voire encrasser les installations. Sans parler du nettoyage de fond de cuve, qui envoie un flux concentré à la fois en graisses et en détergents…
.jpg)
CMI Proserpol propose également d’isoler les flux les plus concentrés afin de les traiter à part. « Nous avons réalisé une installation pour Saint Louis Sucre, près de Caen. Les effluents dilués vont en traitement aérobie, et les plus concentrés sont dirigés vers une filière parallèle, en attendant l’installation d’une méthanisation » explique ainsi Antoine Lemaire. Même problématique chez McCain, qui traite des pommes de terre et génère donc des effluents fortement chargés en amidon. Dans l'usine Mc Cain d'Harnes CMI Proserpol traite les déchets concentrés en amidon, graisses et pelures dans un méthaniseur dont la fraction liquide rejoint une Step aérobie classique traitant aussi les effluents dilués issus du procédé.
Nereus a intégré dans son ADN le tri des déchets liquides, et non pas leur traitement : le fractionnement par un procédé innovant des composés constituants les différents effluents municipaux, agricoles et industriels rend leur valorisation plus facile et efficace. Sur une laiterie de l’ouest de la France, la solution Recynov®, développée par Nereus, a été mise en œuvre sur le site (eaux blanches, condensats), démontrant que l’autosuffisance en eau est accessible tout en générant 6,2 GWh/an soit plus de 20 % des besoins annuels en gaz de l’usine.
.jpg)
Ovive pratique aussi la séparation des effluents en fonction de leur charge organique, afin de ne pas se trouver en situation de sur-dimensionner la STEP. Les flux très chargés peuvent soit être dirigés vers une filière propre, soit stockés dans un bassin tampon et relargués vers la STEP à un rythme qu’elle peut supporter. « Nous avons mis en place un système de ce type chez un industriel de la pharmacie, dont certaines eaux de premier lavage sont très fortement chargées en matières organiques. Nous avons installé un capteur, un COTmètre, sur le canal d’évacuation de ces unités. En fonction d’une valeur définie en DCO, un automate envoie le flux vers la station ou vers un bassin tampon » explique Maxime Pollet. Ovive met en œuvre le même “COTmètre” chez une société d’embouteillage de boissons sucrées.
Ces flux surchargés en matière organique peuvent même constituer… un réactif pour d’autres stations d’épuration ! C’est ce qu’explique Maxime Pollet : « en tant que traiteurs d’eau, nous sommes aussi consommateurs de pollution. En traitement biologique, pour rééquilibrer le rapport carbone/azote/phosphore, nous sommes parfois amenés à ajouter de la DBO. L’effluent fortement concentré d’un industriel peut ainsi être valorisé en réactif pour une autre installation. Nous le faisons par exemple à partir d’une sucrerie, avec le jus de premier rinçage des cuves, que nous utilisons comme réactif sur d’autres stations ».
Les solutions se développent
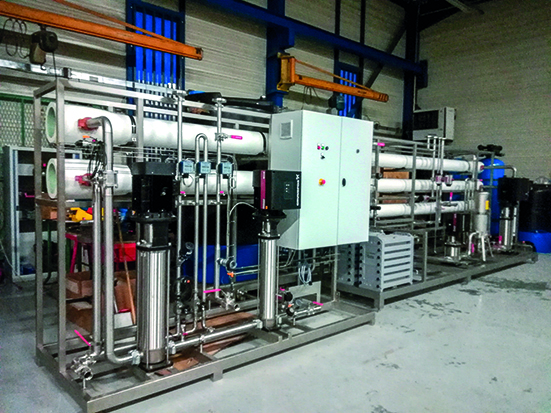
Poussant la logique de séparation jusqu’au bout, BWT développe un trieur d’effluents automatisé, capable d’identifier en continu les eaux réutilisables/recyclables et celles qui doivent être envoyées sur la station d’épuration. « Nous plaçons des capteurs de DCO, ou d’autres paramètres, dans les flux et c’est la corrélation entre différents indicateurs qui permet de faire tri des effluents. Nous collaborons avec Aquassay pour la partie récupération et mise en forme des données » précise Thomas Féron. Un essai industriel de plusieurs mois dans une importante laiterie française vient de montrer que le système est parfaitement capable de trier des condensats de laiterie. Après validation de ces essais, le trieur sera lancé commercialement durant 2019. « Nous avons fait des essais en laboratoire et savons que le système est adaptable en sucrerie, en industrie chimique… En fait, si on a les capteurs, il suffit de choisir les paramètres à suivre et de faire la bonne courbe d’étalonnage. On saura alors trier n’importe quel effluent » affirme Thomas Féron.
Traitement de surfaces : un cas à part…
CMI Proserpol, spécialiste historique de ce domaine, collabore de longue date avec la société lyonnaise Sleti (qui a depuis intégré le groupe CMI), laquelle fabrique des chaines de traitement de surfaces. « Quand un industriel créée une nouvelle usine, il n’a pas toujours l’expertise pour savoir quelle pollution en sortira. Or c’est ce qui détermine le dimensionnement de la station de retraitement. CMI Proserpol a cette expertise. Dans ce domaine, c’est donc nous qui calculons les données de base » explique Antoine Lemaire. Les effluents peu concentrés des bains de rinçage peuvent soit être envoyés à la station, soit recyclés. Ils sont alors traités localement, au niveau des ateliers, en passant sur des résines. « La station ne reçoit alors que les éluats de régénération des résines. Cette manière de concentrer localement la pollution avant de l’envoyer vers le traitement final réduit énormément les quantités à traiter, donc la taille de la station » précise Antoine Lemaire. La question du dimensionnement de la station de traitement devient même cruciale avec l’arrivée de projets “zéro rejet”. En effet, au “classique” traitement final physico-chimique se substitue alors une évapo-concentration. « Il faut optimiser les flux pour évaporer le moins possible car l’évaporateur est déterminant dans le coût de la station » souligne Antoine Lemaire. Intervenant beaucoup dans le domaine aéronautique, CMI Proserpol a par exemple récemment dirigé un groupement d’entreprises CMI (Proserpol, Sleti et Europe Environnement) pour définir et réaliser un atelier complet de traitement de surfaces pour Airbus Hélicoptères à Dugny, près du Bourget. Dans cette installation “zéro rejet”, avec recyclage des eaux vers le procédé (après déminéralisation), tous les flux sont séparés dès la source.
Hytec Industrie, aujourd’hui membre du groupe Aquaprox, intervient sur ce marché depuis plusieurs décennies. « La séparation des flux est nécessaire de par la nature chimique et la concentration de ces effluents, mais aussi du fait que ces derniers sont souvent générés à des moments différents dans la journée ou dans la semaine et peuvent varier. Les rinçages, peu concentrés, sont traités classiquement sur une filière physico-chimique adaptée, alors que les bains de traitement doivent être stockés puis soit envoyés à faible débit dans la filière, soit envoyés directement en centre agréé. Ainsi, il n’est pas rare, dans les ateliers de traitements de surfaces, d’avoir plus de 10 réseaux de collecte et autant de stockages qui permettent de mettre en œuvre des prétraitements spécifiques mais aussi d’écrêter les flux à traiter et donc de faciliter l’exploitation des stations », prévient Arnaud Lepoivre, directeur général délégué, chez Hytec Industrie. Le traitement, classiquement mis en œuvre, est constitué de prétraitements spécifiques (cassage acide, déchromatation, décyanuration…) d’une neutralisation, d’une coagulation et d’une floculation, suivies par une séparation liquide-solide par décantation (ouvrage de type lamellaire ou cylindro-conique).
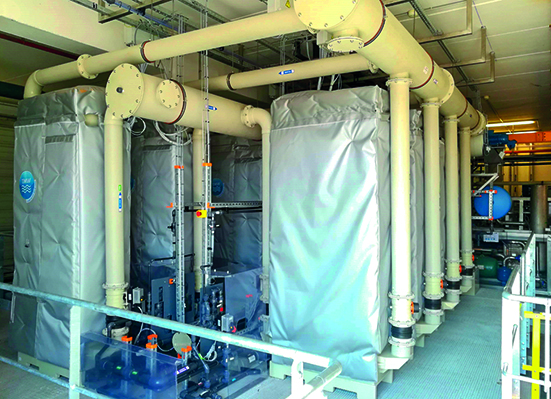
d’effluents issus du traitement de surfaces.
Les exigences industrielles actuelles imposent aux fournisseurs d’agents de conditionnement, des réactifs apportant toujours plus de performance, dans un environnement toujours plus propre. Dans cet esprit, Lhoist a développé Neutralac® SLS45, la chaux liquide concentrée à 600 g/l associant haute réactivité et facilité de mise en œuvre pour optimiser les étapes de neutralisation – coagulation – floculation – décantation ou flottation. « Grâce à sa facilité de stockage, sa précision de dosage et sa réactivité unique, l’industriel dispose d’une chaux liquide toujours disponible et intégrable dans l’automatisme de son procédé », explique-t-on chez Lhoist. Ce réactif breveté s’impose également comme une véritable alternative à la lessive de soude chez les industriels désireux d’effectuer un ajustement pH. L’effluent peut être rejeté directement. Les boues métalliques sont récupérées et déshydratées. Un effluent contenant encore trop de métaux peut alors subir une finition.
Récent acteur français dans le domaine de l’évapo-concentration, TMW, avec sa technologie MHD s’impose progressivement dans le traitement d’effluents issus du traitement de surfaces. Des choix techniques spécifiques et originaux, la différencient des technologies traditionnellement utilisées : une évaporation à pression atmosphérique, dispense cette technologie de tout recours à des pièces sensibles telles que compresseur et pompes à vide ; le recours à des matériaux plastiques, la rend particulièrement résistante aux effluents agressifs. Par ailleurs, la modularité de l’équipement, facilite l’adaptation de la capacité de traitement au besoin du client, dans le temps. « La conséquence globale, est une maintenance très réduite et, par voie de conséquence, un taux d’utilisation de l’équipement maximal. Tout ceci dans un confort opérationnel appréciable du fait de l’absence de nuisances sonores », souligne Thierry Satgé, directeur général de TMW.