Du traitement de surface à la verrerie, en passant par le textile, certains industriels doivent se débarrasser d’effluents non biodégradables. Des solutions de traitement existent pour chaque cas, avec un coût énergétique variable. L’accent est maintenant placé sur la récupération de l’eau, et éventuellement des polluants eux-mêmes.
De nombreuses activités industrielles génèrent des effluents
que la filière d’épuration
biologique classique qu’il s’agisse
de la STEU municipale ou d’une installation propre à l’usine ne peut
prendre en charge. Industries métallurgique et mécanique, traitement de
surface, chimie, textile, production
d’énergie, verrerie, papèterie, microélectronique, entre autres, produisent
des eaux chargées en métaux, sels minéraux et/ou molécules organiques non
biodégradables.
Afin de ne pas dépasser les limites
admissibles de rejet dans le milieu, les
industriels peuvent faire appel à tout un
panel de technologies de traitement de
leurs effluents, aujourd’hui bien maîtrisées. Au-delà des limites réglementaires
sur la qualité des eaux rejetées dans le
milieu, ils sont également contraints par
les tensions sur l’usage de l’eau et le coût
de l’énergie. Certains souhaitent également récupérer des matières d’intérêt
dans les effluents, le «déchet» devenant
alors une ressource. Autant de préoccupations qui pèseront sur le choix de la filière de traitement de leurs effluents.
Dès lors, quelles sont les nouveautés
technologiques dans le domaine? Le
contexte d’utilisation évolue-t-il? Est-il
possible de recycler ces eaux polluées ?
le jeu en vaut-il toujours la chandelle?
BIEN CHOISIR SA FILIÈRE
Traitement physicochimique, oxydation
avancée, résines échangeuses d’ions,
charbon actif, technologies membranaires, évapotranspiration: il existe
des réponses techniques pour chaque
besoin. Certaines seront plus indiquées
pour une dépollution avant rejet vers le
milieu naturel ou la STEU municipale,
d’autres interviennent plutôt comme
traitement complémentaire avant un
recyclage de l’eau épurée. Des constructeurs de solutions ou fournisseurs de
produits comme Adiquimica, Ajelchim,
Aquadep, Aquaprox I-Tech, Atlantique
Industrie, BWT, Chemdoc, CWT Global,
DuPont Water Solutions, Exocell, Messer
France, Nijhuis Saur Industries, Niskae,
Polymem, Séché Environnement, Sahler,
Serpol, TMW, Veolia Water Technologies,
Vivlo ou Waterleau, entre autres, interviennent sur ce marché.
En l’absence de recette standard, la pratique générale est désormais de réaliser
des essais pilotes, au laboratoire ou sur
le terrain, afin de mieux cerner la nature
des effluents, les besoins de l’industriel et
les performances des différentes technologies de traitement avant de définir et
dimensionner la solution adaptée.
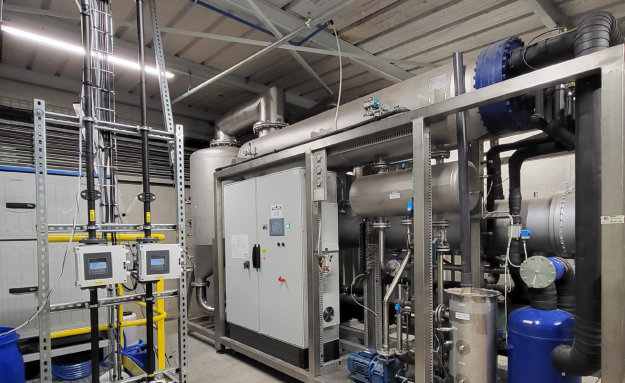
«Nous utilisons toujours notre conteneur pilote Plug & Reuse car ces effluents, par nature variables, nécessitent des essais. Cela nous permet de placer ensuite la bonne technologie au bon endroit» rappelle ainsi Dimitri Monot, responsable de l’activité ReUse chez BWT France. Il cite pour exemple un «petit conteneur» assurant le recyclage de l’eau sortant de la STEU d’une usine aéronautique en Ile-de-France. «Un filtre à sable, une désinfection, et cela suffit pour renvoyer l’eau dans le système de refroidissement du client. Nous avons analysé en amont son effluent et son système de refroidissement, et avons ainsi pu mettre en place cette technologie «légère», là où des concurrents auraient installé des membranes, plus chères et énergivores» explique-t-il. BWT réalise actuellement des essais pilotes pour, entre autres, une usine de production de biocarburant et un producteur d’adjuvants pour l’industrie chimique.
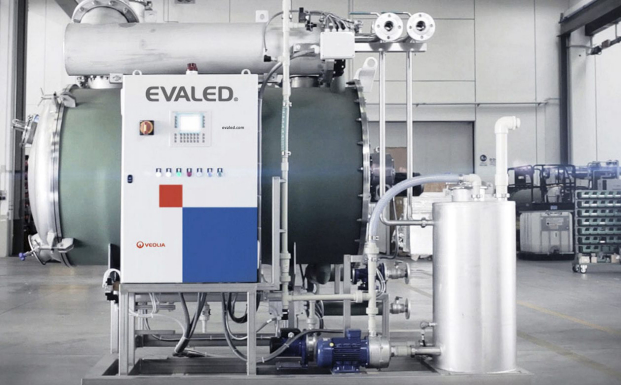
Même démarche d’essais préalables chez Waterleau, par exemple pour les effluents complexes de l’industrie textile. «Ces eaux usées contiennent de la matière organique non biodégradable, par exemple de la teinture, des micropolluants comme l’azote ou le phosphore et, dans une moindre mesure, des métaux lourds. Elles sont de plus très chargées en sels. Nous prévoyons donc systématiquement des essais en laboratoire sur des échantillons d’effluents» affirme Philippe Schnongs, directeur Process chez Waterleau. Avec son bureau d’études et son usine de fabrication basés à Perpignan, Tecnofil Industries intervient également de manière personnalisée pour concevoir des installations de grande envergure ou pour collaborer sur des projets de process skid de toutes tailles, de conception de filtre à l’unité, ou encore de matériel complémentaire pour le fonctionnement d’un site.
Grâce à l’intégration des activités de
services de traitement des eaux industrielles en France de Veolia, le groupe
Séché s’attache également à personnaliser les projets. «Face à la diversité et
à la complexité des solutions techniques
proposées, l’activité Traitement des Eaux
Industrielles de Séché Environnement
est capable d’identifier, de combiner
et de mettre en œuvre les solutions les
plus adaptées, parmi toutes celles disponibles sur le marché, et de s’engager
également sur leurs performances réelles
en exploitation», souligne Christophe
Doublet, directeur opérationnel Séché
Environnement.
DES TECHNOLOGIES MATURES, SOUVENT COMBINÉES
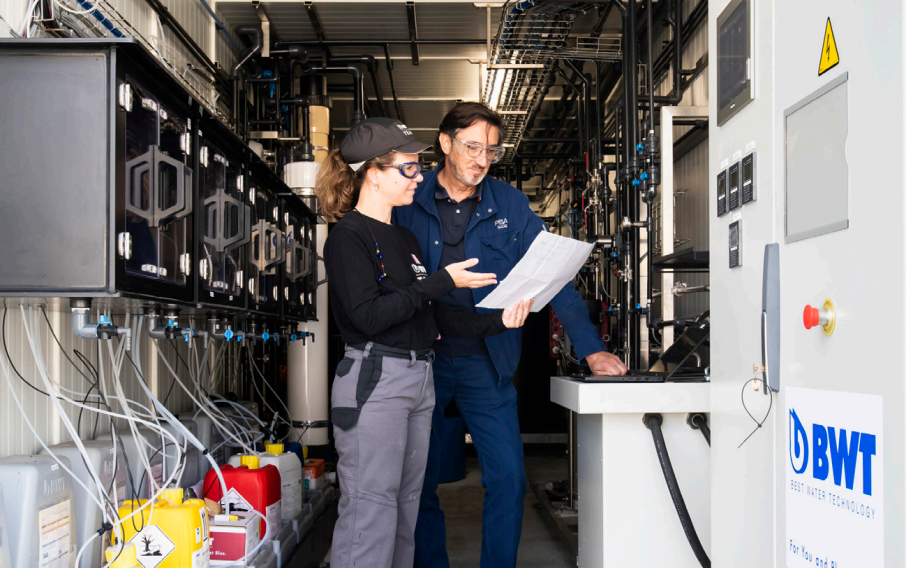
Longtemps la solution reine, et encore bien souvent installé en début de filière, le traitement physicochimique décantation, coagulation-floculation, flottation, sédimentation… atteint parfois ses limites face à une réglementation de plus en plus exigeante. Il consomme également des produits chimiques (coagulants, floculants…). «Le procédé devient rapidement complexe à gérer si, par exemple, l’effluent contient plusieurs métaux. De plus il génère de grandes quantités de boues d’hydroxydes métalliques qu’il faut ensuite déshydrater et évacuer» ajoute Frédéric Fuhrmann, Responsable Marchés Reuse & Recycle France chez Veolia Water Technologies. «Nous installons de moins en moins de STEU purement physicochimiques, même pour rejeter les effluents dans l’environnement. Lorsqu’on nous le demande, la filière physicochimique est complétée par un traitement de finition. Il s’agit d’améliorer la captation des polluants pour atteindre ou dépasser les normes de rejet» confirme Matthieu Delaunay, responsable commercial Eaux résiduaires chez Aquaprox I-Tech.
La société vient par exemple d’achever, chez un fabricant de granulés de plastique, la phase d’essais pilotes pour une filière physicochimique (par flottation) complétée par un filtre à sable et du charbon actif. «L’idée est de fournir une solution assez souple pour pouvoir, à court ou moyen terme, intégrer une partie de recyclage de l’eau» précise Matthieu Delaunay. Pour oxyder chimiquement les polluants organiques réfractaires à la biodégradation, la société d’ingénierie Actibio met en œuvre le procédé d’oxydation avancé Fenon qui utilise du peroxyde d’hydrogène et un catalyseur comme le fer pour générer des radicaux hydroxyles très oxydants, fait remarquer Jean-François Berenger.
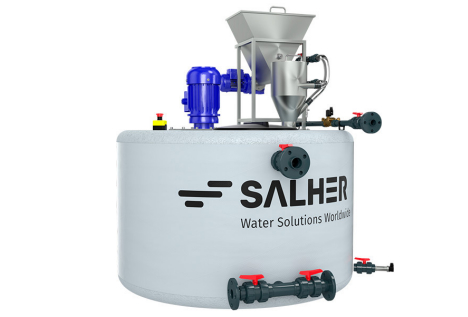
«Ces radicaux attaquent les composés organiques et diminuent fortement la DCO tout en rendant biodégradables les composés résiduels». À l’autre extrémité du spectre, l’évapoconcentration est souvent convoquée en fin de traitement pour concentrer au maximum le déchet final à évacuer. Elle est par ailleurs indispensable aux démarches de type «zéro rejet liquide» (ZLD pour zero liquid discharge). Son tendon d’Achille est évidemment sa consommation d’énergie. «Nous proposons lorsque c’est possible des évaporateurs hybrides qui fonctionnent à l’énergie thermique «gratuite» la chaleur fatale récupérée sur les fours, compresseurs, ou autres dispositifs du site industriel complété éventuellement par une pompe à chaleur. Il s’agit d’économiser l’énergie au maximum. Nous allons lancer une première installation de ce type sur un très gros tunnel de traitement de surface en région lyonnaise» révèle Julien Brochier, directeur commercial de Vivlo.
La société développe actuellement une dizaine de projets sur ce modèle d’énergie thermique. Bien souvent, la bonne solution ne consiste pas à choisir une technologie dans le panel disponible mais à en combiner plusieurs. Matthieu Delaunay (Aquaprox I-Tech) cite par exemple une importante réalisation dans la Sarthe. «Notre client, fabricant d’équipements à usage unique pour les secteurs médicaux, prévoit de réutiliser les effluents de sa STEU. Nous avons proposé une solution multiétage, combinant traitement physicochimique, traitement biologique, traitement de l’azote, ultrafiltration, charbon actif et ozonation. Le tout sur un débit de 40 m3 /h» explique-t-il.
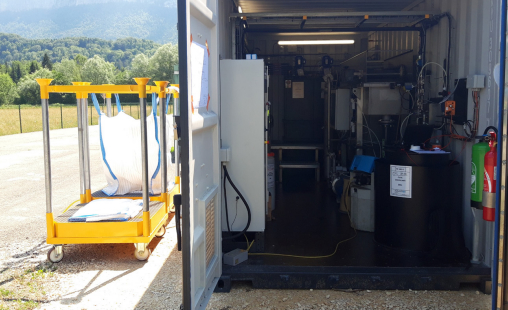
Niskae, en tant que fabricants de produits coagulants et floculants spécifiques, commercialise une gamme de microstations physico-chimiques pour le traitement et le recyclage des effluents. «Niskae se concentre sur le développement de formulations floculantes ciblées combinées à notre gamme de microstations. Nous sommes ainsi en mesure de traiter un large spectre d’effluents industriels avec un procédé physico-chimique de nouvelle génération hautement efficace qui réduit les dosages et le nombre des réactifs utilisés. Les niveaux d’efficacité constatés notamment en termes de réduction des niveaux de DCO, d’azote et de phosphore, permettent de limiter le dimensionnement des traitements de finition souvent consommateurs de matériaux et parfois énergivores» expose Julien Quiblier, associé fondateur de la société.
A titre
d’exemple, chez un fabricant d’enveloppes et de pochettes dont les eaux
usées présentent des concentrations en
fer et une DCO élévée, après plusieurs
batchs de traitement de 500L, l’installation de la microstation SW500 qui combine floculation, filtration/déshydration
au travers d’un big-bag+ filtre charbon
permet d’assurer la mise en conformité
du rejet. Salher, de son côté, indique
avoir investi d’importantes ressources
pour l’optimisation des processus de
potabilisation en ajoutant notamment
des systèmes de prétraitement chimique
avant la phase de potabilisation.
Le fabricant recommande tout particulièrement son équipement physicochimique Vespa, qui comprend une
unité de préparation automatique du
polyélectrolyte. «Cette combinaison
de prétraitement chimique, ou traitement physico-chimique, avec les stations d’épuration biologiques de Salher
permettent non seulement de contrôler
la consommation d’énergie, mais aussi
de réduire le volume des équipements,
facilitant ainsi les tâches de contrôle et
de maintenance des stations d’épuration
des eaux usées industrielles», résume
Christina Alda, responsable marketing.
DES FIBRES PROMETTEUSES
Une nouvelle venue vient de s’ajouter à la gamme déjà étendue des solutions de traitement. Elle est basée sur des matériaux filtrants composés de fibres polymères, développés et produits par Ajelis, une start-up conjointe du CEA et de l’Université Paris-Sud. Leur intérêt: des performances d’épuration très supérieures à celles des résines ou du charbon actif, et la possibilité d’adapter spécifiquement les fibres à chaque polluant. A tel point que Chimirec, une société bien connue d’enlèvement et traitement des déchets, s’est associée à Ajelis pour fonder Ajelchim en février 2023 afin de commercialiser ces matériaux et des solutions basées sur ceux-ci auprès des industriels ou des sociétés d’ingénierie.
Initialement développées pour les métaux lourds (nickel, cuivre, zinc, plomb, chrome…), ces fibres peuvent être adaptées à de nombreux polluants. «Nous venons d’achever une campagne d’essais sur des effluents contenant du nickel cyanuré. Notre matériau peut en effet décomplexer des composés non traitables actuellement par les résines ou le charbon actif. En un seul passage, nos fibres ont abaissé la teneur de 31 mg/l à 1,2 mg/l, et l’industriel a passé une commande à Ajelchim» explique par exemple Ekaterina Shilova, fondatrice et PDG d’Ajelis. «Nous allons mettre en route des essais auprès d’une STEU qui ne peut pas épandre ses boues car elles contiennent du cadmium. Nous pourrons le capter spécifiquement et rendre les boues valorisables en agriculture» ajoute Johann Daniel, directeur des filiales de traitement et directeur technique de Chimirec, qui envisage aussi une utilisation sur les effluents industriels colorés (encres, teintures…).
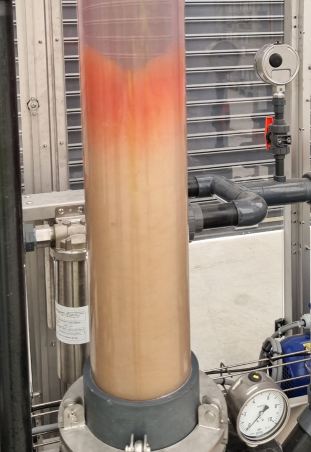
Chimirec utilise d’ores et déjà ces matériaux dans son propre centre de Paimbœuf (Loire-Atlantique), qui traite 20000 tonnes de déchets liquides par an, pour enlever le chrome des eaux polluées avant leur passage dans une filière plus classique d’épuration. Ajelchim commercialise les cartouches de matériau soit directement auprès des industriels qui les installent dans leur process, à charge pour Chimirec de les récupérer puis les régénérer, soit auprès de sociétés d’ingénierie qui les intègrent à des solutions complètes de traitement des effluents. «Nous pouvons régénérer les cartouches au moins une centaine de fois nous ne savons pas encore jusqu’où avant de les remettre à disposition. Certains clients, en particulier les chimistes qui ont le savoir-faire nécessaire, peuvent d’ailleurs le faire euxmêmes, ce qui produit tout de même un déchet (acide, soude) que Chimirec prend en charge» explique Johann Daniel.
Outre les cartouches, Ajelchim propose d’ores et déjà une machine standard plug and play, la CHIMICAPT® Box. Cette «boîte» (2m x 2m X 1m) munie de tuyaux d’entrée et de sortie et d’un raccord électrique (220V) peut traiter 5 m3 /h de liquide pollué. «Elle répond aux normes CE, est totalement sécurisée et autonome. Un néophyte peut l’utiliser» soutient Johann Daniel. Face à la demande, Ajelchim va développer des unités plus importantes et polyvalentes. Ces solutions peuvent s’utiliser soit seules, soit en complément d’une STEU existante ne pouvant plus faire face à des exigences réglementaires renforcées. Elles peuvent aussi se combiner avec des résines. «En associant résines et fibres, on peut fiabiliser et sécuriser l’ensemble du process. Les résines fonctionnent en effet en «tout ou rien»: elles perdent très rapidement leur efficacité lorsqu’elles sont saturées. Or on ne sait pas prévoir exactement ce moment, d’où des problèmes réguliers de non-conformité des effluents. Les fibres, plus robustes, peuvent «encaisser» ces à-coups et lisser le résultat. De plus, elles captent les polluants jusqu’à des concentrations dix fois inférieures à ce qu’atteignent les résines» affirme Johann Daniel.
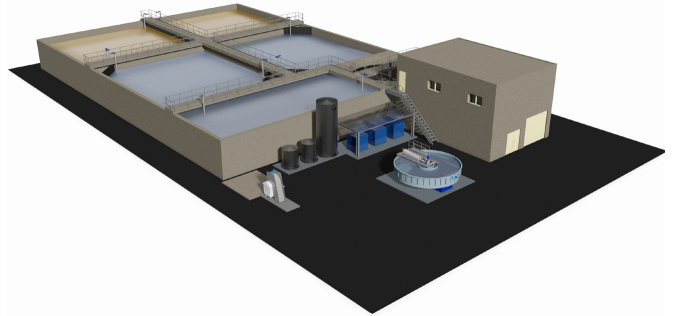
«Traiter les effluents industriels,
c’est toujours du sur mesure et c’est même
plus compliqué quand il faut traiter des
batchs de différentes qualités confirme
Nicolas Meudal, fondateur de la société
1h2o3 GmbH. Nous avons développé la
mini-STEP qui regroupe un bassin tampon, 4 technologies conventionelles et un
traitement des boues. Elle est conçue de
sorte à ce que chaque technologie puisse
être combinée à une autre. Ainsi, il est
possible de déterminer quel est le procédé
le plus adapté pour l’effluent à traiter.
Les clients choisissent le plus souvent la
location avec option d’achat, ce qui leur
permet d’acheter la mini-STEP si elle
est suffisante pour atteindre les performances recherchées ou de la remplacer
par le procédé correctement dimensionné
grâce aux résultats des essais sur site».
RÉUTILISER L’EAU TRAITÉE
Contraintes sur la ressource aidant, de moins en moins de projets de traitement d’effluents industriels se conçoivent aujourd’hui sans la possibilité de réutiliser au moins une partie de l’eau traitée (REUT). D’autant que le décret du 29 août 2023 «relatif aux usages et aux conditions d’utilisation des eaux de pluie et des eaux usées traitées», abrogeant celui du 10 mars 2022, simplifie l’instruction des dossiers, supprime la limitation des projets à 5 ans et augmente les volumes d’eau réutilisables. La REUT est toutefois encore restreinte aux usages non alimentaires : au moment où nous mettions sous presse, le décret complémentaire portant sur ces derniers usages, tant attendu par l’industrie agroalimentaire, n’était pas encore publié. Si le principe est adopté par tous, reste à déterminer, au cas par cas, la rentabilité de l’opération.
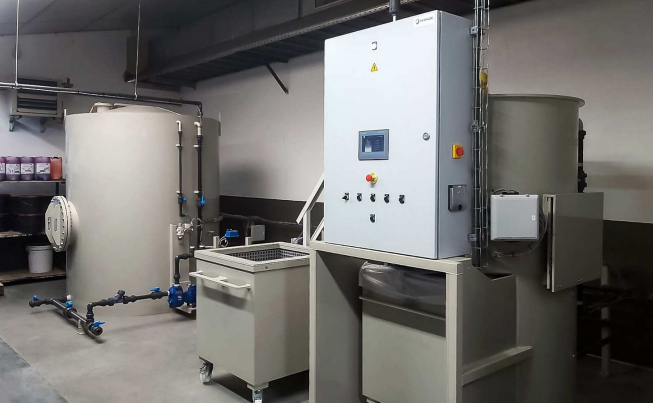
La REUT, impliquant des technologies membranaires et/ou l’évapoconcentration, est en effet énergivore. Veolia Water Technologies vient par exemple d’équiper un site de l’industrie automobile en Pays de Loire, rejetant après sa STEU un flux important (près de 2000 m3 /an) d’eau traitée contenant encore des métaux, des hydrocarbures et une charge organique. «Jusqu’alors, ils éliminaient leurs effluents en centre extérieur. Nous avons mené une étude et ils nous ont commandé une unité d’évapoconcentration de type pompe à chaleur PCF6AA ainsi qu’un post traitement Aquadem composé de charbon actif pour les résidus organiques et de résines échangeuses d’ions pour l’ion ammonium. Le volume de concentrat à évacuer est 15 fois moindre qu’avant, et le reste de l’eau (environ 93% du volume initial) est intégralement réutilisé pour la chaudière du site. C’est une eau déjà chaude et déminéralisée, ce qui convient parfaitement à cet usage. Entre les économies d’énergie, d’eau et de tonnage de déchets à évacuer, le retour sur investissement sera très rapide» estime Frédéric Fuhrmann.
Veolia propose également une gamme allant de 5 à 30 m3 /h de solutions membranaires conteneurisées prêtes à l’emploi, destinées à se placer en aval d’une STEU (physicochimique et/ ou biologique) pour affiner l’eau traitée avant réutilisation dans le process ou les utilités. Le premier conteneur, consacré à l’ultrafiltration, est équipé de membranes ZeeWeed adaptées aux effluents industriels. Le deuxième contient une unité CaptuRO™ d’osmose inverse, et un troisième est consacré au stockage/dosage des produits de nettoyage des membranes et au monitoring. «Nous avons développé cette gamme standard à partir de notre retour d’expérience européen. Elle convient à toutes les industries et correspond à un marché croissant depuis un an» affirme Frédéric Fuhrmann. «Environ 80% des demandes de solutions de traitement comportent un volet de recyclage» estime pour sa part Matthieu Delaunay (Aquaprox I-Tech).
Sa société fournit des clients dans l’armement, l’aéronautique, l’automobile ou le luxe (bijouterie ou dépose de métaux précieux), entre autres. Les solutions proposées dépendront du volume à traiter. «Dans l’aéronautique, les volumes sont modestes et nous proposons plutôt des solutions de recyclage court, après une étude préalable de l’outil de production. L’automobile produit en revanche des volumes conséquents d’effluents et les sites disposent en général d’une STEU physicochimique. Nous installons alors plutôt des membranes spéciales en aval de la STEU, en combinant ultrafiltration tangentielle et osmose inverse, pour faire de la réutilisation partielle. Le concentrat d’osmose est mélangé au reste du rejet. On peut aller plus loin encore avec un évapoconcentrateur mais il ne faut pas négliger le bilan carbone de l’ensemble» souligne Matthieu Delaunay. Aquaprox I-Tech installe actuellement une solution membranaire en aval de la STEU physicochimique et biologique d’une usine de cosmétiques.
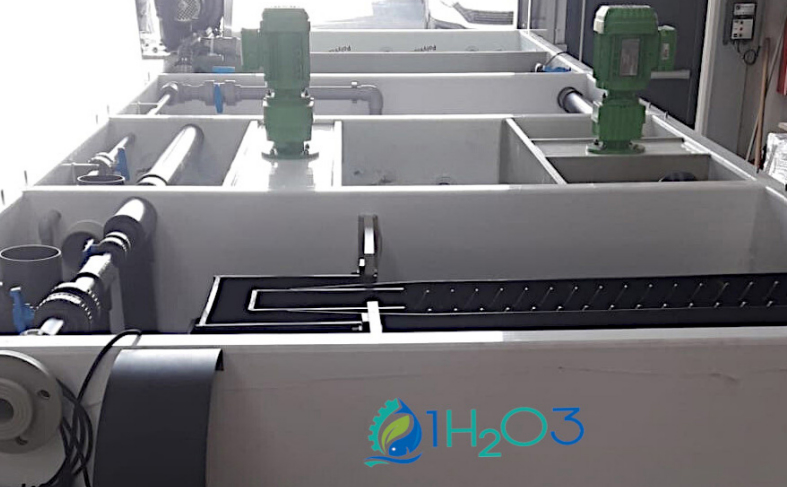
L’eau sera ensuite désinfectée pour
retourner au process.
BWT a pour sa part lancé un essai pilote
chez un industriel de la mécanique souhaitant recycler à la fois les eaux de
purge de sa TAR et les effluents de sa
STEU physicochimique. Le faible volume
d’eau de bonne qualité provenant de la
TAR est d’abord mélangé aux effluents
beaucoup plus importants, et très chargés, de la STEU. L’ensemble est alors
traité par une combinaison d’ultrafiltration et d’osmose inverse. «Au final,
nous recyclerons 15000 m3
/an» prévoit
Dimitri Monot.
Les spécialistes de la désinfection de
l’eau comme Bio-UV, Trojan ou UvRer
pour ne citer qu’eux ne sont pas en reste.
Adapté au domaine de la chimie, UVrer
a développé un pilote semi-industriel
sur-mesure qui intègre tous les éléments nécessaires au fonctionnement
du process sur skid (réacteurs UVc,
pompe, filtration…). «En collaboration
avec de grands comptes de la chimie,
nous développons des procédés permettant le traitement de nombreux polluants
chimiques et notamment les complexes
organométalliques. En effet, certaines
méthodes de traitement conventionnelles
ne permettent pas le traitement des
métaux lorsqu’ils sont sous forme de complexes avec des composés organiques»,
commente Kamal Rekab, responsable
R&D chez UVrer.
ZÉRO REJET LIQUIDE : UNE OPTION ENCORE RARE
Réutiliser toute l’eau usée pour ne rejeter finalement qu’un effluent extrêmement concentré, voire un déchet solide… L’idée du ZLD est séduisante sur le papier mais implique un recours quasi systématique à l’évapoconcentration, avec la consommation énergétique que cela suppose. Cette option n’est donc pas forcément adaptée à toutes les situations. «Pour l’instant, le ZLD très rarement utilisé en France, sauf en cas de fortes contraintes» affirme ainsi Laurent Moncho (Waterleau).
Reste que certaines branches industrielles y ont plus volontiers recours. Matthieu Delaunay (Aquaprox I-Tech) cite par exemple l’armement et l’aéronautique. «En traitement de surface dans ces branches, nous proposons une évapococentration pour les bains chargés et le recyclage sur résine pour les derniers rinçages» explique-t-il. De par son domaine d’intervention privilégié, les industries mécaniques et le traitement surface, Vivlo est également amené à proposer des solutions de ZLD.
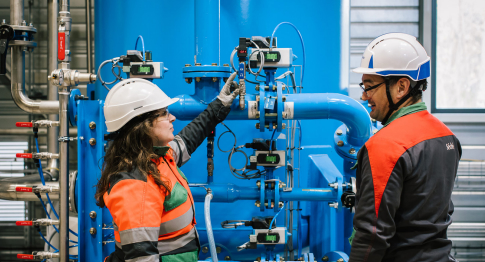
«Nous parvenons parfois à n’évacuer qu’un déchet solide, grâce à un fonctionnement différent de l’évaporateur et, surtout, un conditionnement particulier de l’effluent à évaporer. Au final, nous arrivons à une solution ZLD ayant des coûts de fonctionnement inférieurs à un traitement physicochimique» affirme Julien Brochier (Vivlo).
Après un premier essai en traitement de surface il y a trois ans, Vivlo reproduit actuellement le procédé à grande échelle en région lyonnaise. De la directive ZLD, TMW en a fait un argument fort de son évapoconcentrateur Ecostill, qui associé à un pilotage process et un data monitoring ajusté en temps réel doit améliorer l’efficacité hydrique et énergétique des différents flux. «On doit considérer l’ensemble des options et des flux: re-use ou économie d’eau de process, mais aussi la valorisation du concentrat et de toutes les matières qu’il contient. C’est sur l’ensemble de la chaîne que nous souhaitons donc accompagner nos clients» précise Guilllaume Bourtourault, nouvel actionnaire et président de TMW.
ET LES MATÉRIAUX ?
Par définition, les effluents sont des eaux chargées de polluants. Les séparer pour récupérer l’eau propre est une démarche évidente, mais les «polluants» euxmêmes peuvent présenter un intérêt. Si le jeu n’en vaut pas la chandelle pour le fer, des éléments comme le titane, le chrome, le nickel ou le magnésium peuvent être intéressants à récupérer. Sans compter les métaux précieux… «En traitement de surface, l’argent, l’or et le palladium sont systématiquement récupérés via des électrolyseurs traitant le concentrat d’évaporation. Nous venons par exemple de réaliser une installation en ZLD traitant l’intégralité du cyanure d’argent afin de récupérer ce dernier» affirme ainsi Matthieu Delaunay (Aquaprox I-Tech).
«Nous recevons des
demandes de récupération du lithium.
L’idée est de concentrer l’effluent jusqu’à
obtenir un extrait sec. Pour cela, nous
utilisons une première évapococentration classique allant jusqu’à la limite de
précipitation, suivie d’un évaporateur
cristalliseur pour une valeur d’extrait
sec supérieure à 75%» explique pour sa
part Frédéric Fuhrmann (Veolia Water
Technologies).
Ajelchim envisage également ce type
d’opération. «L’objectif ultime est de
transformer l’eau polluée en eau propre
et produits purs. Nous menons des programmes de recherche en ce sens. La
force d’Ajelis est de pouvoir créer des
fibres extrêmement sélectives, pouvant isoler un élément déterminé. On
peut ainsi faire passer un effluent successivement sur différentes fibres pour
purifier les éléments d’intérêt. Au lieu
d’obtenir un mélange concentré, on a
des extraits purs» affirme ainsi Johann
Daniel (Chimirec). La société envisage
aussi la récupération des catalyseurs au
nickel ou au vanadium, des déchets polluants qui peuvent ensuite être réactivés
et redevenir des produits.