Très grands consommateurs d’eau, les industriels de l’agroalimentaire se questionnent sur la réutilisation des eaux usées traitées. En France, le cadre réglementaire freine les initiatives. Pourtant, des solutions existent pour pouvoir réutiliser cette ressource que ce soit pour l’irrigation, les utilités ou même dans le process
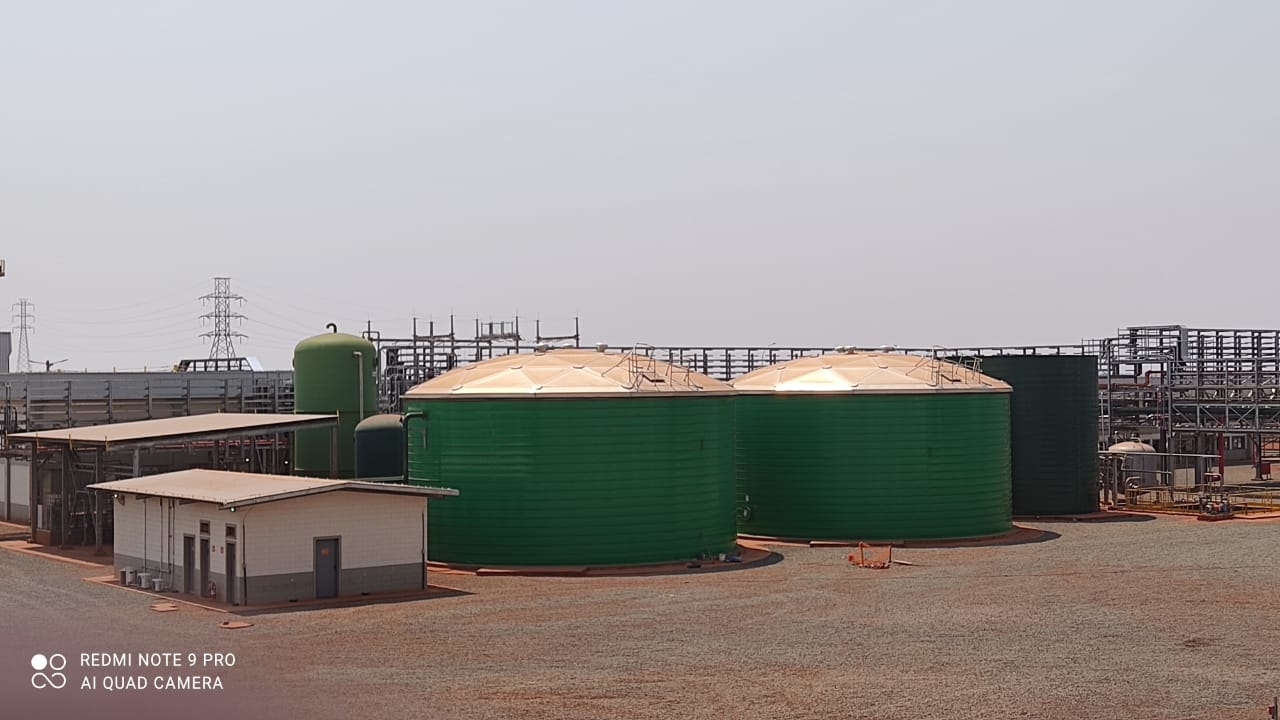
Même s’il est techniquement possible de traiter ces effluents jusqu’à la potabilité, il est interdit en France de réutiliser pour une production alimentaire une eau qui a légalement un statut de déchet. Le cadre général n’existe pas. Les industriels de l’agroalimentaire doivent le plus souvent solliciter le cadre local pour pouvoir réutiliser leurs effluents traités.
Certaines DREAL commencent toutefois à demander des plans concrets pour maîtriser la consommation et les rejets dans l’agroalimentaire. Des projets sont en cours d’études, certains sites industriels font l’objet d’expérimentation de la part de l’administration, soutenus par les agences de l’eau. « La réutilisation est un sujet prégnant. Le stade de la R&D est dépassé, il faut désormais plus de démonstrateurs sur site pour inciter les industriels à participer aux économies de la ressource », considère Pierre-Yves Rioual.
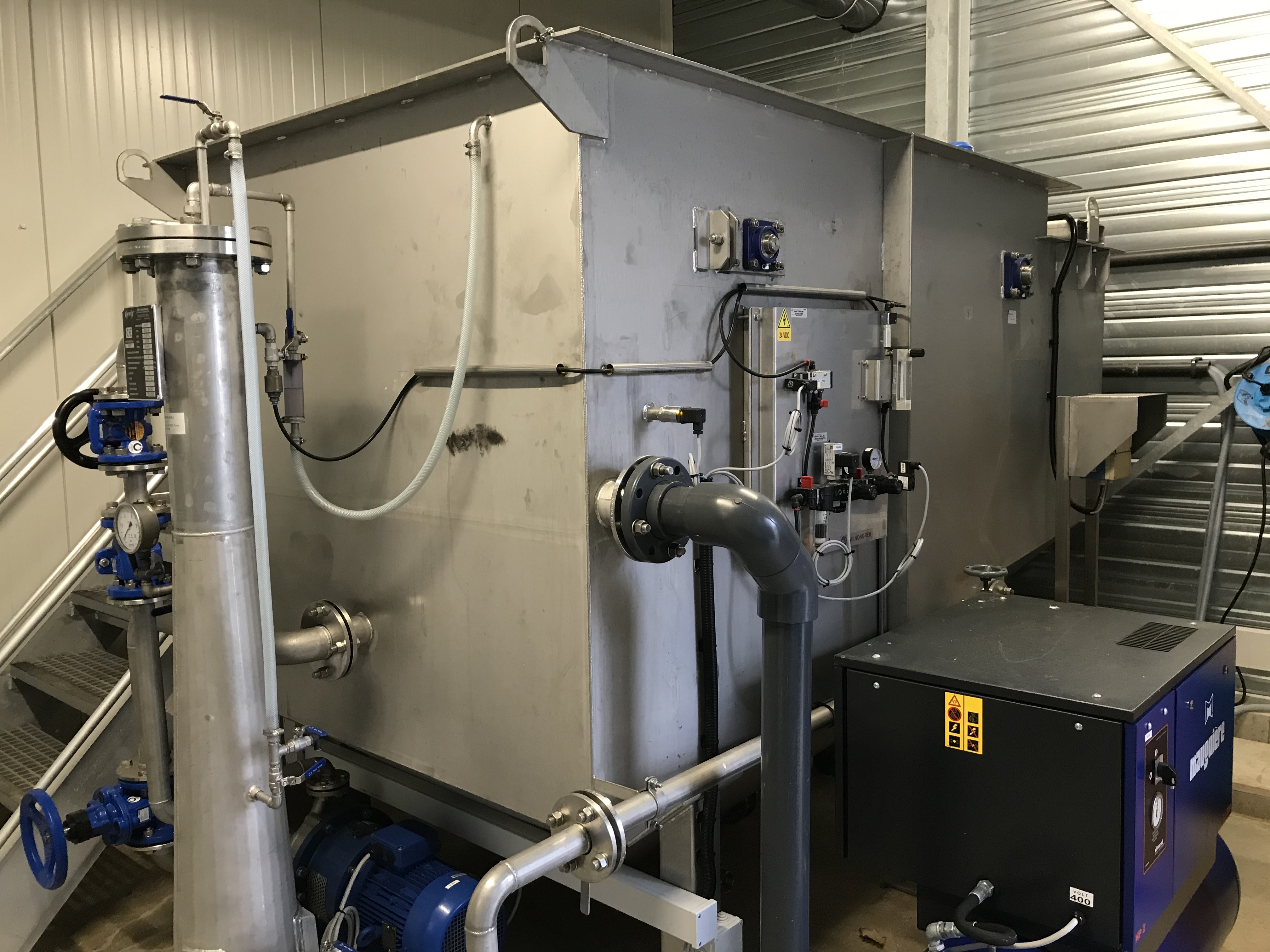
« Le recyclage d’un effluent de process n’était pas autorisé par le Code de la Santé Public (CSP) jusqu'en 2018, commente Julien Louchard, formateur en traitement et valorisation des effluents industriels à l’OIEau. Depuis, la nouvelle version de l'article L1322-14 du CSP a ouvert les perspectives à la Reut pour les entreprises alimentaires. La réutilisation d'eau devient possible si la qualité des eaux n'a aucune influence, directe ou indirecte, sur la santé de l'usager et sur la salubrité de la denrée alimentaire finale. Cette opportunité n'a pourtant pas permis une mise en application et pour cause : le décret en conseil d’État qui doit déterminer les dispositions à mettre en œuvre, n’a toujours pas été publié. Des projets de démonstration existent d'ores et déjà et devraient permettre de montrer l'exemple ».
Des solutions de traitement déjà disponibles
« Nous avons plusieurs installations membranaires pour du recyclage d’eaux (eau de process, eau industrielle usée…) dans des industries agroalimentaires, à l’étranger, rappelle Isabelle Duchemin, Marketing & Commercial Manager Polymem. Les réglementations sont moins restrictives et permettent la limitation des rejets en les réutilisant. En découlent également des économies d’eau et un impact minimisé sur la ressource en eau. Nous avons par exemple travaillé sur un système membranaire chez un producteur de chips en Australie. L’objectif est de traiter de l’eau usée de procédé issue du lavage des pommes de terre et friteuses pour atteindre une eau de qualité alimentaire pour réutilisation. Une chaîne de traitement d’eau complète incluant des skids d’ultrafiltration et d’osmose inverse permettent cette production d’eau. Très récemment, nous avons également travaillé pour un embouteilleur pour la réutilisation des eaux usées traitées (post phytoépuration) pour l’économie d’eau potable dans l’usine. L’eau ultrafiltrée ira alimenter les sanitaires de l’usine en eau potable. L’eau économisée permettra d’embouteiller plus d’eau, puisqu’il s’agit de la même ressource ».
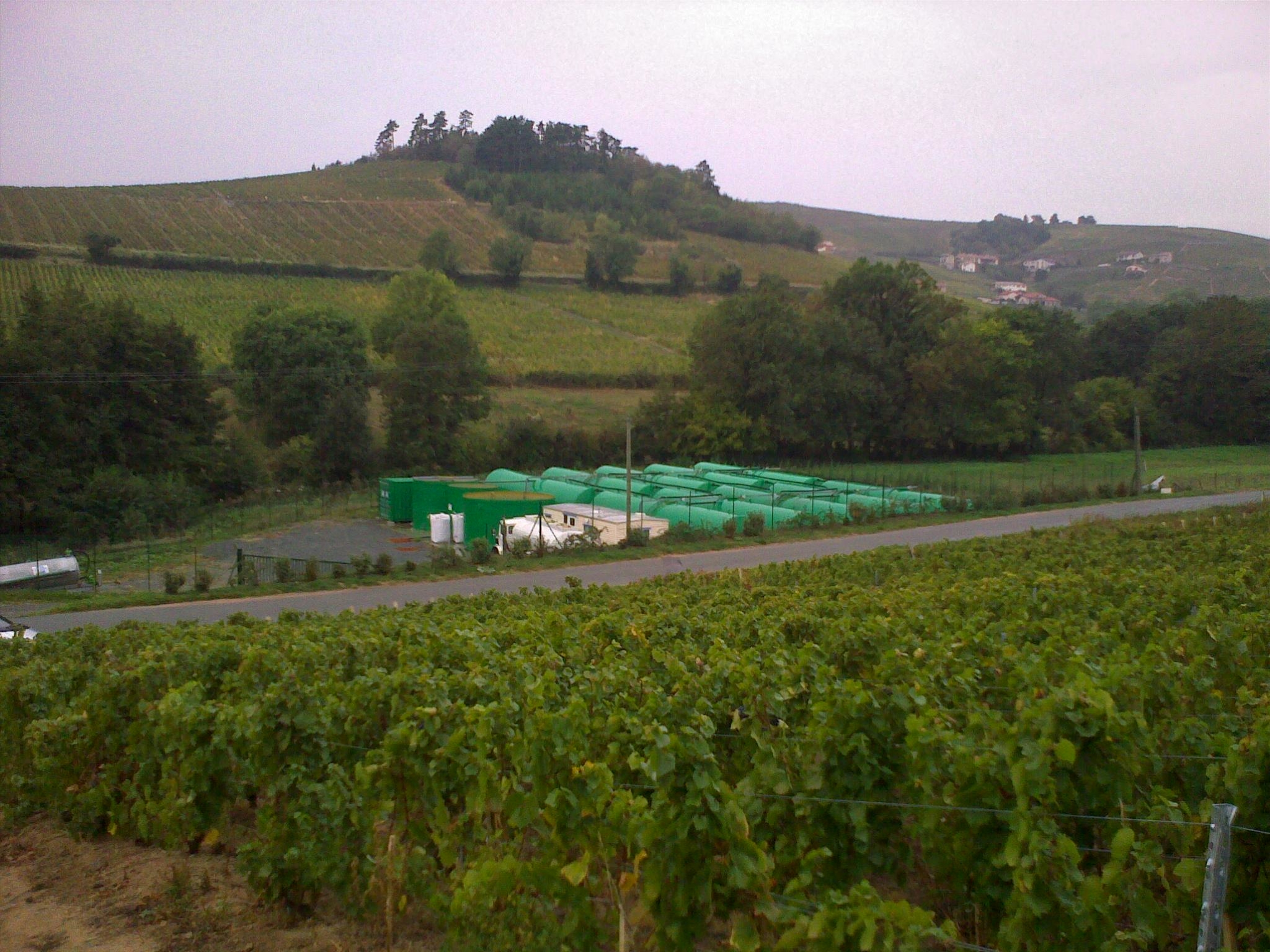
En Europe, l’Espagne comme la Belgique se démarquent des autres pays de l’Union. Plus grand consommateur d’eau par habitant avec l’Italie et le Portugal, le pays dispose de deux fois moins de ressources en eau moyennes annuelles qu’en France. Ses besoins concernent principalement l’agriculture, notamment l’irrigation des cultures. « L’Espagne est un très bon élève de la réutilisation. Les industriels chez qui nous intervenons proviennent essentiellement du secteur viticole. Tous ou presque utilise de l’eau recyclée pour l’irrigation de leurs vignes », souligne Pierre-Yves Rioual. Soumises aux mêmes directives européennes, la réutilisation des eaux usées traitées issues de l’industrie agroalimentaire n’est pas autorisée dans le processus de production. « Ces eaux usées épurées peuvent être rejetées sans contaminer, ou être utilisées pour des travaux de nettoyage dans l’industrie, pour le lavage de machines, l’arrosage des jardins ou l’eau des toilettes par exemple », résume Cristina Alda, responsable marketing chez Salher.
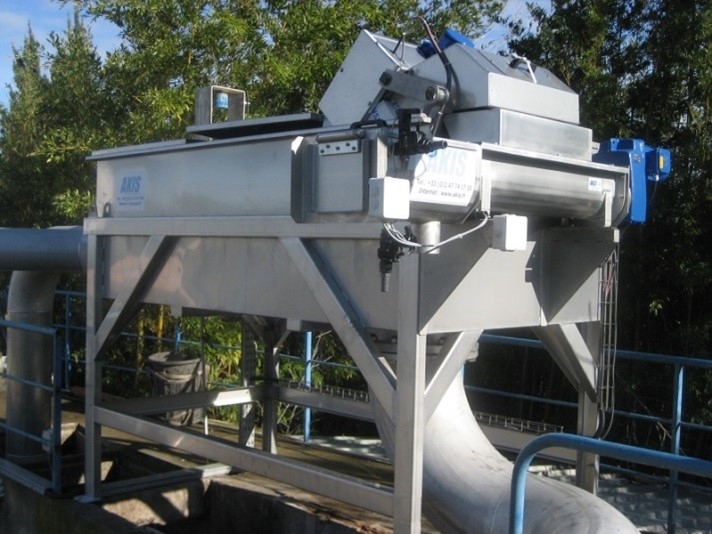
Polymem adapte également son process en fonction de la qualité de l’eau entrante et celle attendue en sortie, confirme Isabelle Duchemin « Parfois l’ultrafiltration suffit car elle clarifie et désinfecte l’eau en une seule étape. Nous utilisons alors nos modules Gigamem, très compacts, avec notre fibre Neophil en PVDF à hydrophilie durable dans le temps. Neophil présente des rétentions (bactéries, virus…) et des performances identiques sur membranes neuves et vieillies, ce qui fiabilise le traitement et rassurent les industriels sur la longévité de l’installation. Nous pouvons également proposer en complément des systèmes de nanofiltration et osmose inverse ».
Parmi les spécialistes de la séparation et du transfert des fluides, Alfa Laval propose une solution membranaire BRM déjà en place sur différents site agroalimentaires français permettant le rejet des eaux traitées dans les cours d'eau. Ailleurs dans le monde, leurs systèmes d'évapo-concentration permettent à leurs clients d'atteindre le rejet liquide nul (zero liquid discharge).
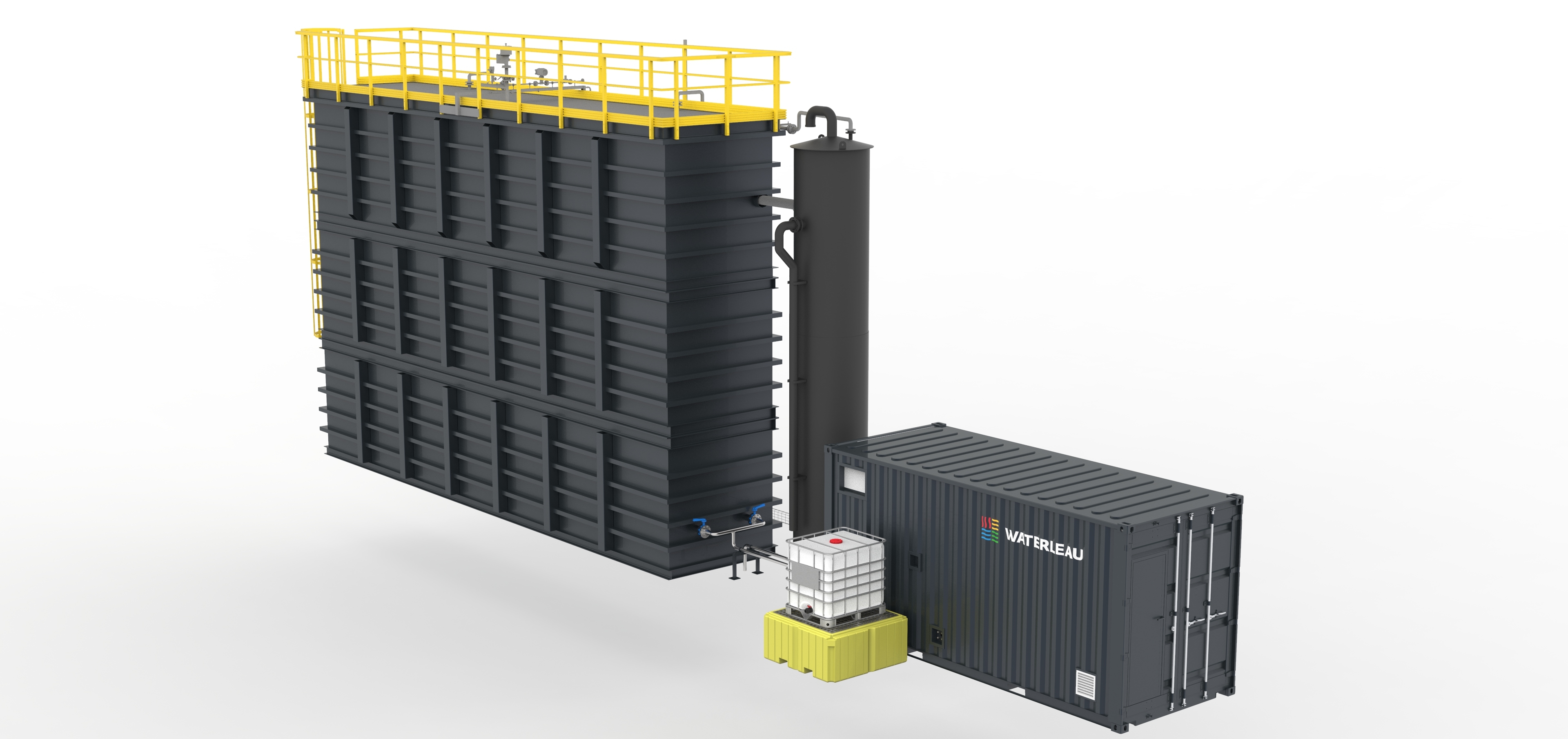
Avec quelques 1 600 projets développés à travers le monde, Veolia Water Technologies n’est pas en reste sur la compréhension des enjeux des entreprises agroalimentaires, en tous genres et de toutes tailles. En Afrique du Sud, l’installation complète de l’usine de lait de Nestlé que WTS a réalisée, incarne la stratégie “zero water discharge” emblématique du secteur, notamment dans le domaine “alimentation et boissons”. Située en aval de l’usine de Mossel Bay, l’unité́ de traitement réceptionne les eaux usées acheminées par adduction gravitaire en provenance des stations de lavage et des zones de nettoyage des ateliers de poudre de lait et de lait concentré sucré. La nouvelle installation de traitement et valorisation des effluents comprend un réservoir d’acidification, un digesteur anaérobie, des plates-formes d’ultrafiltration et d’osmose inverse, une chaudière à biogaz et des équipements auxiliaires. A Poperinge en Belgique, le spécialiste de la transformation de pommes de terre, Aviko, a donné le coup d'envoi des travaux de sa nouvelle unité de production. Il a retenu les équipes de Veolia Water Technologies pour traiter l’ensemble des polluants (DCO, azote et phosphore) tout en valorisant les effluents en biogaz. Le traitement anaérobie des effluents est basé sur la conversion des polluants organiques en biogaz. Pour ce faire, Veolia Water Technologies, utilise le procédé de méthanisation par voie granulaire Biothane Advanced UASB.
Économiser la ressource et réduire les coûts
Pour les effluents vinicoles ou les vinasses, Aderbio propose la station de traitement biologique STBR1 qui consiste dans un prétraitement à partir de la fosse de stockage tampon, suivi d’une succession d’opérations de traitement en cuves séparées : digestion bactérienne aérobie, précipitation, décantation et filtration. « La décantation est assistée par un précipitant naturel qui améliore les qualités mécaniques et agronomiques des boues. Notre procédé breveté de Bio-augmentation permet de limiter le volume des boues à moins de 0,5 % des volumes traités. De ce fait leur épandage n’est recommandé que tous les 4 ou 5 ans. L’effluent traité est apte au rejet en milieu naturel, il peut aussi être utilisé pour l’arrosage ou le lavage du matériel », rappelle Olivier Poline, directeur général chez Aderbio.
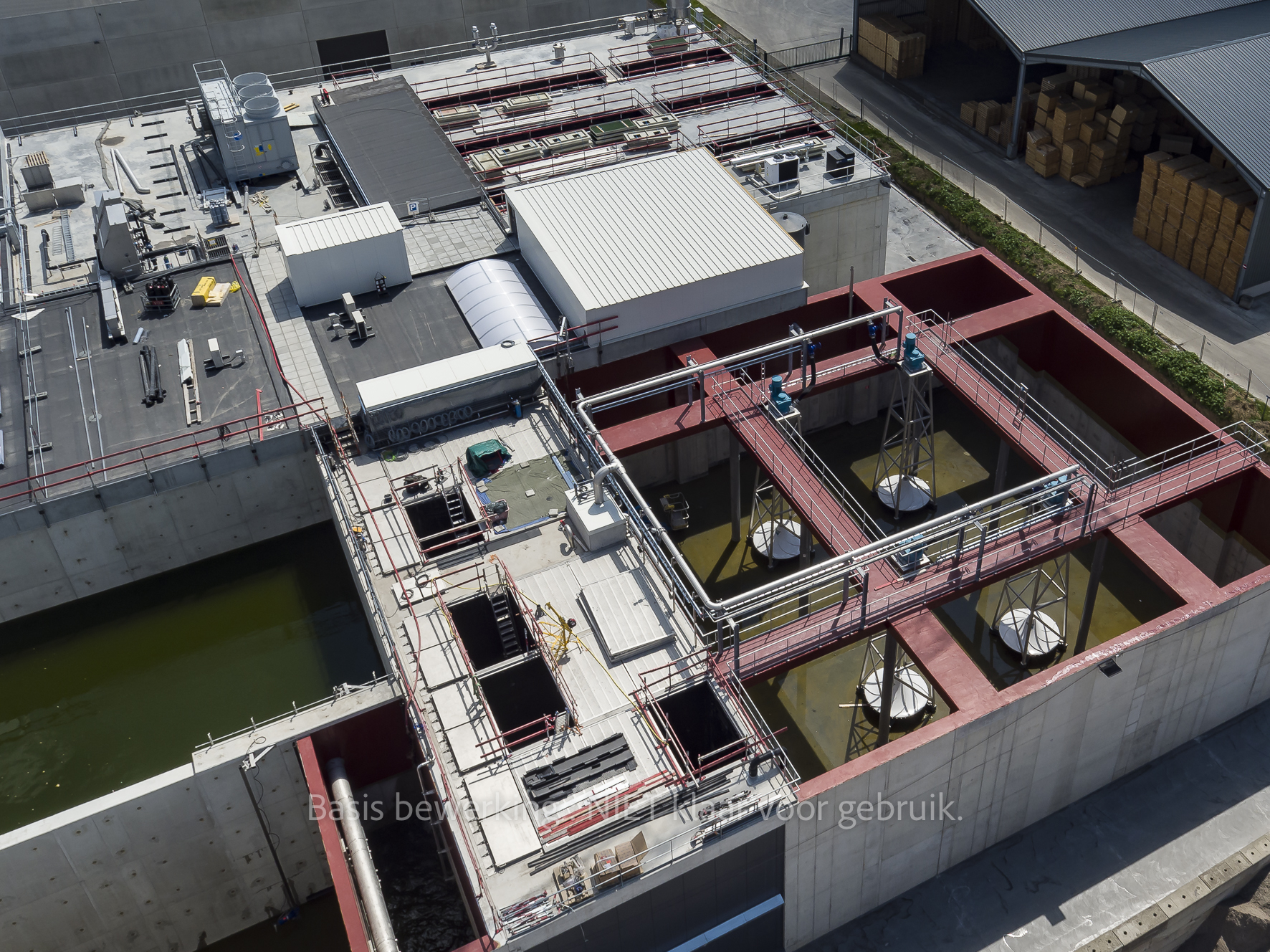
Cohin Environnement propose également de plus en plus son procédé biologique séquentiel et continu UniBiocell en filière de traitement des effluents agroalimentaires. « Le fonctionnement en trois étapes de traitement dans un seul et même bassin regroupant la phase de traitement biologique, la phase de décantation et la phase de rejet favorise les projets à forte compacité ou ayant un concept de modularité avec le produit Waste Water Box. Les rendements épuratoires très performants de ce procédé permettent à ces industriels de limiter leur coût de redevance pollution lorsqu’ils sont connectés sur le réseau d’eaux usées ou d’avoir des performances de traitement assez poussées pour rejeter les eaux traitées dans le milieu naturel. Les principaux avantages de la solution brevetée par Cohin Environnement reposent sur la compacité de l’installation et les coûts d’exploitation optimisés. Le système est également capable d’atteindre des abattements suffisants pour pouvoir également réutiliser ces eaux à des fins industrielles avec l’addition de technologies de filtration ou solutions membranaires » assure Sandrine Noël, responsable commerciale.
Nombre de fabricants, concepteurs et réalisateurs de projets clés en main se sont mis à proposer des nouvelles installations requérant notamment une faible emprise au sol et un fonctionnement simplifié. On peut citer Atlantique Industrie, FBI Biome, John Cockerill, Nereus, Ovive, Polymem ou Waterleau notamment.

Chez KWI, 80 % des stations d’épuration clé en main concernent le secteur agroalimentaire. « Les flottateurs constituent le cœur de métier de notre entreprise. Le choix de cet équipement en traitement primaire est presque systématique chez nos clients ; notre procédé de traitement physico-chimique par flottation Ecocell garantit en effet de très bons rendements pour épaissir les graisses et réduire les volumes d’eau en vue d’une valorisation énergétique par méthanisation », affirme Christophe Dedieu, directeur général chez KWI France.
En 2019, Salher a développé le procédé DAF Vespa : un flottateur à air dissous qui permet d’éliminer jusqu’à 90 % des matières en suspension, des particules sédimentaires, des huiles et graisses, pour une réduction des valeurs de DB05 et de DCO de l’ordre de 50 % à 80 %. « Grâce à notre nouveau flottateur, les traitements biologiques sont beaucoup plus efficaces et les rendements d’élimination plus élevés, de sorte que, dans certains cas, nous pourrons éliminer certains traitements ultérieurs », poursuit Cristina Alda.

Pour répondre au besoin de traitement de l’eau en continu exprimé par l’usine Nature de Volvic (groupe Danone) en 2018, les équipes d’ingénierie de projet BWT ont recommandé une solution de désinfection à l’ozone, produit à partir de l’oxygène présent dans l’air ambiant. Trois ans plus tard, l’ozoneur permet de traiter l’eau des rinceuses, stockée dans deux cuves de 50 m³ et d’alimenter en eau de process le réseau de l’usine Fruit, pour une réutilisation dans les CIP (Cleaning In Place - pour nettoyer les circuits), la stérilisation et les rinçages entre les différentes recettes de boissons. Le principe de l’installation repose sur une boucle de recirculation qui permet d’assurer une ozonation de l’eau en continu, tandis qu’un passage sur UV, permet d’éliminer les traces d’ozone et ainsi obtenir une eau limpide totalement exempte de goût ou de résidus de produits chimiques. Au total, 380 millions de litres d’eau ont pu être économisés de 2017 à 2020 pour des volumes de productions stables.