L’évaporation sous vide apporte des réponses à des problématiques industrielles plus que jamais d’actualité, telles que la maîtrise des coûts de l’énergie, le traitement des effluents, la réduction du volume de déchets. Grâce à des résultats éprouvés au fil des dernières décennies, et aux innovations qui lui permettent de s’améliorer, elle constitue toujours une solution essentielle pour les industriels de différents secteurs.
INTRODUCTION
Dans son principe de fonctionnement, l’évaporation sous vide consiste notamment à extraire de l’eau propre d’une part, et à concentrer les polluants d’autre part, en reproduisant sous vide et à basse température les phénomènes se produisant d’ordinaire avec une pression atmosphérique «normale». Son utilisation repose donc sur l’utilisation d’un vide plus ou moins poussé qui va diminuer la température d’évaporation (entre 30° et 85°) et donc le point d’ébullition. Selon la nature et l’encrassement du produit, la valorisation d’énergie recherchée ou encore le type de machine que l’on utilise, le vide créé sera donc variable. Dans ce domaine, différents fabricants tels que Veolia Water Technologies, H2O, TMW, Vivlo, Kmu Loft ou Leviathan Dynamics s’emploient à innover dans les deux grandes sous catégories qui régissent le principe de l’évaporation sous vide, à savoir la compression mécanique de vapeur ou les pompes à chaleur.
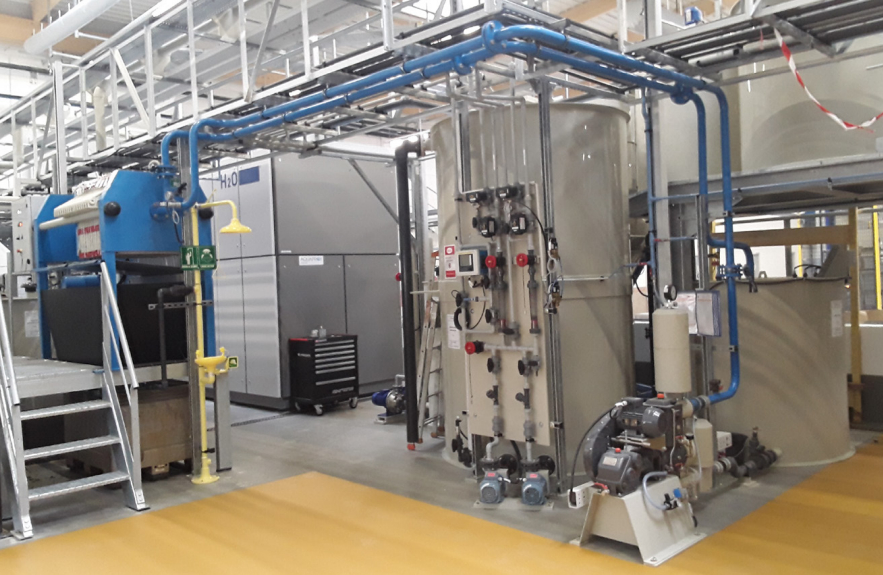
Les acteurs du secteur sont nombreux, notamment les intégrateurs,
qui les combinent aussi souvent avec
d’autres procédés et proposent diverses solutions, avec des entreprises telles
que Exonia, FE Group (ex-France
Evaporation), Aquaprox I-Tech,
Buchi, Ecobome Industrie, ou encore
Fbi Biome.
Au cours des dernières décennies, l’évaporation sous vide n’a cessé d’évoluer,
devenant indispensable pour garantir
des processus industriels plus propres
et durables. Confrontés à des exigences
réglementaires et économiques toujours
plus pressantes, les professionnels du
traitement des eaux et des effluents
s’appuient sur des innovations variées
en matière de compression mécanique
de vapeur et de pompes à chaleur.
Aujourd’hui, des solutions de plus en plus
sophistiquées, permettent de combiner
efficacité énergétique et adaptabilité à
des flux d’effluents variés.
L’ÉVOLUTION DES ÉVAPORATEURS : DES DÉCENNIES D’INNOVATIONS TECHNIQUES
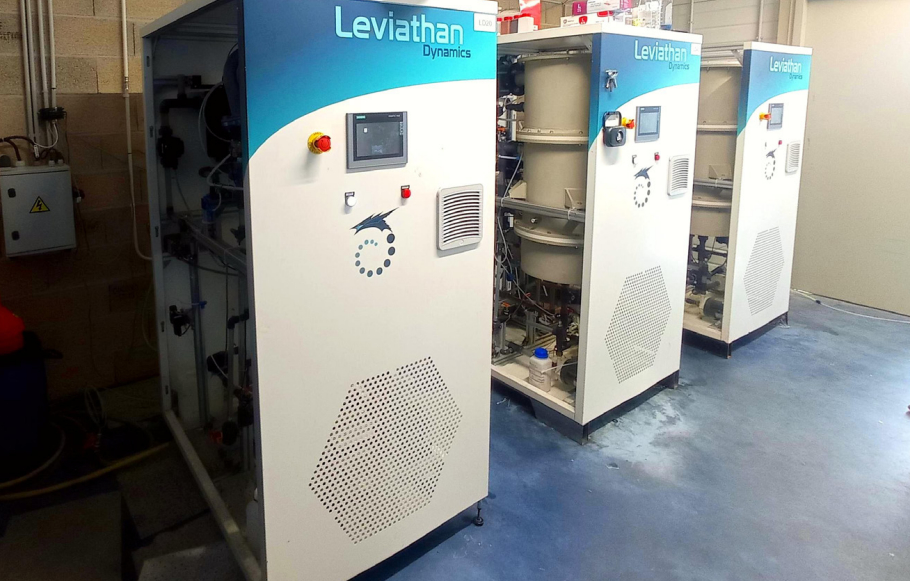
Depuis une trentaine d’années, les évaporateurs ont donc connu une évolution significative, portée par des progrès technologiques constants et des innovations notables. Chez Aquaprox I-Tech, par exemple, le déploiement de cette technologie a commencé il y a plus de 25 ans avec une première installation marquante pour Alcatel Vacuum Technology. Cette intégration a permis de mettre en place un atelier de traitement de surface en zéro rejet complet, témoignant ainsi des grandes ambitions et des capacités d’adaptation des évaporateurs sous vide dès leurs débuts. Jean-Lin Laurouaa de Kmu Loft et Frédéric Fuhrmann de Veolia Water STI s’accordent à dire que les évaporateurs sous vide se sont affinés au fil des décennies, notamment grâce à l’optimisation continue des technologies de compression mécanique de vapeur (CMV) et des pompes à chaleur (PAC). Jean-Lin Laurouaa affirme que «les évaporateurs sont aujourd’hui en compétition directe avec d’autres technologies comme le membranaire, le biologique et le physico-chimique», tandis que Frédéric Fuhrmann souligne que Veolia «a réduit de manière assez conséquente la consommation énergétique des installations par rapport à celles d’il y a 30 ou 40 ans».
CHOIX STRATÉGIQUE : ADAPTER LA TECHNOLOGIE AUX DÉFIS DE L’EFFLUENT
Mathieu Delaunay, de chez Aquaprox I-Tech, affirme que la sélection de la technologie d’évaporation sous vide la plus adaptée repose d’abord sur un savoir-faire précis qui prend en compte la nature des effluents à traiter, ainsi que les objectifs économiques et énergétiques des industriels, qui déterminent «la technologie d’évaporateur la plus adaptée à l’effluent par rapport à ce que l’on veut en faire». La distinction entre les technologies réside principalement dans l’optimisation énergétique et la compatibilité avec les flux d’effluents spécifiques. JeanLin Laurouaa de chez Kmu Loft note que «parmi les évaporateurs sous vide il y existe des sous-catégories : la compression mécanique de vapeur ou la pompe à chaleur à très basse température». Il précise que la compression mécanique de vapeur (CMV) travaille à environ -400 millibars et 80 degrés Celsius, offrant une haute efficacité pour des opérations à température élevée et vide moyen. «Si pour des raisons process, on veut éviter d’aller à haute température, il est également possible d’évaporer à un vide plus poussé de -900mbar, à 40°C. Les évaporateurs utilisant une pompe à chaleur fonctionnent sur ce régime, mais cette technologie est énergivore», précise Karino Kang chez Leviathan Dynamics a justement travaillé sur des évaporateurs qui couple les avantages de la CMV et de la pompe à chaleur.
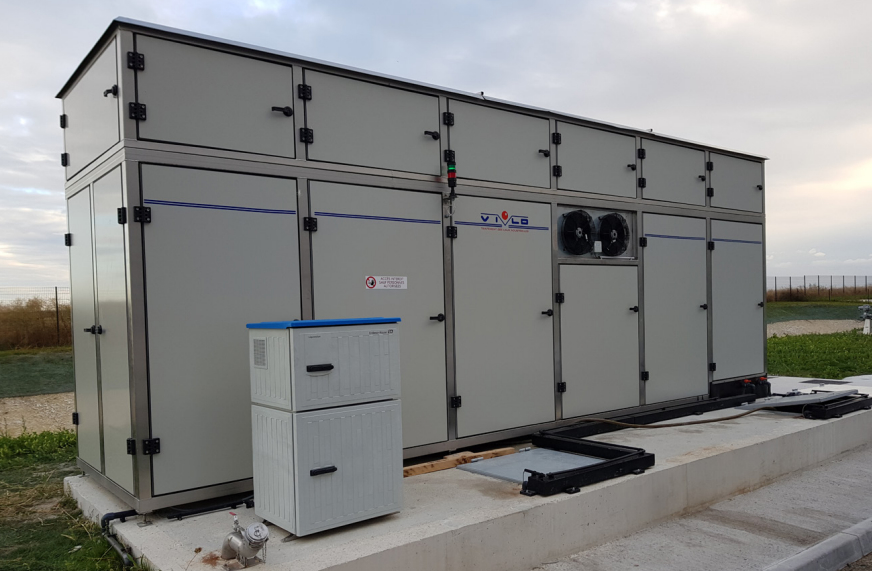
Le TURBEVAP de Leviathan Dynamics est un évaporateur à CMV qui peut évaporer à -900mbars. «Grâce à ce travail à basse température (40°C), la consommation énergétique de l’évaporateur est divisée par 2 par rapport à une évaporation à 80°C», ajoute-t-il. Mathieu Delaunay souligne également que pour des petits volumes évaporés, «il est plus intéressant de passer sur une pompe à chaleur», notamment en raison des coûts de maintenance potentiellement moins élevés des systèmes sans compresseur mécanique. Cependant, pour des volumes plus importants, autour de 100 litres par heure ou plus, la CMV prédomine en raison de son rendement énergétique supérieur. Frédéric Fuhrmann de Veolia Water STI apporte une confirmation de cette approche en expliquant que leur gamme EVALED inclut des évaporateurs à compression mécanique de vapeur, qui fonctionnent à 700 millibars et 90 degrés, pour des flux significatifs. Il insiste aussi sur l’importance des prétraitements et des post-traitements pour garantir l’efficacité de ces systèmes, en précisant que «l’évaporateur permet de traiter majoritairement tous les sels, les métaux, etc.», nécessitant des traitements adaptés en amont pour des effluents spécifiques tels que des éléments huileux ou gras.
Ces choix technologiques sont guidés par divers critères, notamment la consommation énergétique, la compatibilité avec les flux d’effluents particuliers, et les coûts opérationnels. Ces choix stratégiques sont également orientés par des exigences spécifiques en fonction des clients. Alain Dehay précise que «ce n’est pas la technologie qui doit imposer la pression/température de fonctionnement, mais le produit du client». Pour ce faire, FE Group conçoit ses unités en fonction de la nature du produit à traiter et des besoins de valorisation énergétique, tout en assurant des performances optimales dans des configurations sous vide ou à pression atmosphérique. Les propos de Dominique Buzare de AFIG’EO Engineering résonnent particulièrement ici: «Nous faisons beaucoup de prétraitement avant ces évaporateurs… Tout cela pour optimiser complètement les coûts d’investissement et de fonctionnement de l’utilisateur final».
La société TMW propose quant à elle la technologie d’évaporation EcoStill, qui s’apparente à un séchage des effluents liquides. Celle-ci utilise de l’air sec pour évaporer l’eau contenue dans l’effluent, avec une évaporation se faisant en moyenne à 55°C, tandis que l’effluent ne dépasse pas 85°C. «Tout se fait à pression atmosphérique, évitant l’utilisation d’un compresseur bruyant et sensible à la chimie. C’est ce qui nous permet d’utiliser des modules d’évaporation en plastique et sans aucune machine tournante : dans les modules, les écoulements se font par gravité à pression atmosphérique et relativement basse température, il n’y a pas de contrainte de pression ou d’étanchéité à l’air. En fonctionnant largement en dessous de la température d’ébullition, on évapore moins de polluants et on évite le moussage», explique Guillaume Bourtourault, dirigeant de la société basée à Angers où elle fabrique ses évaporateurs depuis 10 ans.
Ici, le processus de récupération de
chaleur est essentiellement assuré par
des échangeurs en composites développés et fabriqués par TMW. En outre,
les pompes à chaleur utilisées pour le
chauffage complémentaire tirent leur
énergie de la déshumidification de l’air
de travail, et ne sont donc pas en contact
avec l’effluent.
«Nos évaporateurs sont insensibles à la
corrosion acide, basique ou saline, grâce
à une conception entièrement composite. L’autre grande particularité de la
technologie tient dans sa modularité :
nous avons différents modules capables
d’évaporer entre 1 et 6 m3
/jour et nous
assemblons jusqu’à 12 modules dans un
EcoStill pour atteindre la capacité souhaitée. Cette modularité permet aux
installations d’être évolutives et la maintenance module par module ne nécessite aucun arrêt de l’évaporateur», ajoute
Guillaume Bourtourault.
PRÉTRAITEMENT INTELLIGENT : RÉDUIRE POUR MIEUX ÉVAPORER
Avant d’envisager l’évaporation sous vide, le prétraitement des effluents est une étape cruciale pour optimiser les coûts énergétiques et accroître l’efficacité globale du procédé. Dominique Buzare d’AFIG’EO Engineering explique: «Nous faisons beaucoup de prétraitement avant ces évaporateurs. On va faire de la précipitation, neutraliser des fluors, on va utiliser plutôt de l’acide sulfurique que de l’acide chlorhydrique». Le prétraitement, en réduisant les volumes d’effluents à évaporer et en limitant la charge polluante, permet une meilleure performance de l’évaporateur et des économies significatives sur la consommation d’énergie. Mathieu Delaunay d’Aquaprox I-Tech renchérit en soulignant l’importance de la préconcentration: «L’idée est d’abord d’avoir des étapes de traitement qui vont préconcentrer au maximum l’effluent, avec une autre technologie que de l’évaporation… on consomme moins d’énergie, et l’on utilise un évaporateur plus petit».
Les techniques de préconcentration telles que l’osmose inverse ou l’utilisation de résines échangeuses
d’ions permettent de réduire significativement le volume des effluents à
traiter par évaporation, diminuant par
conséquent les coûts énergétiques et
opérationnels.
Julien Brochier de Vivlo explore aussi les
bénéfices des configurations d’évaporation multiples, adaptées à la nature des
effluents traités : «Toujours de l’évaporation sous vide mais multiple effet, où
l’on va avoir des niveaux de vide différents, avec des températures d’ébullition
plus élevées». Ce type de configuration
permet d’optimiser non seulement la
consommation d’énergie en utilisant les
vapeurs produites par les premiers effets
pour réchauffer les suivantes, mais aussi
de gérer les comportements différents
des effluents à des températures variées,
assurant ainsi une meilleure qualité de
traitement et une efficacité accrue.
EFFICACITÉ ÉNERGÉTIQUE : LES NOUVEAUX HORIZONS DE LA DURABILITÉ
Depuis la création des premières unités d’évaporation il y a plus de 30 ans, les préoccupations autour de la consommation énergétique n’ont cessé de croître. Initialement, l’idée de diminuer la consommation énergétique faisait déjà partie intégrante des conceptions, à l’instar des systèmes de pompe à chaleur utilisés dès les années 90, mais les progrès étaient limités. Dominique Buzare d’AFIG’EO Engineering partage une analogie pour illustrer le principe: «Nous créons une cocotte-minute mais qui va marcher à l’envers, à la différence que l’on fait le vide au lieu de faire monter la pression à l’intérieur». Les technologies modernes exploitent des principes similaires mais avec des améliorations substantielles. JeanLin Laurouaa de Kmu Loft explique que les innovations récentes incluent des dispositifs permettant d’atteindre des performances énergétiques accrues.
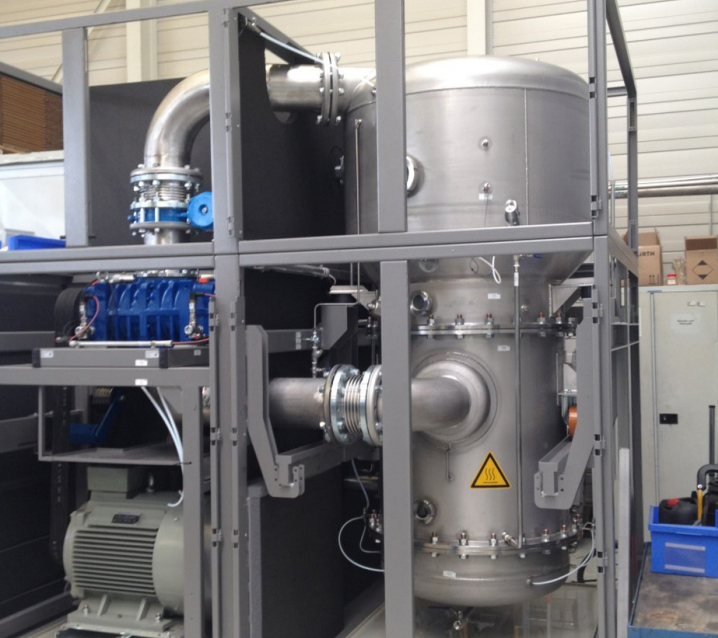
Un mécanisme essentiel est la compression mécanique de vapeur (CMV), qui consomme autour de 40 à 80 kilowattsheure par mètre cube, contre 180 à 250 kilowatts-heure pour les pompes à chaleur. Karino Kang précise qu’avec la nouvelle génération d’évaporateurs CMV sous vide poussée, la consommation est encore réduite à 45kWh/m3 pour les petits évaporateur et à 25kWh/m3 pour les gros évaporateurs. Mathieu Delaunay d’Aquaprox I-Tech souligne l’importance de la sélectivité en fonction des volumes et des composants spécifiques des effluents. Plus récemment, l’orientation vers des solutions hybrides, combinant énergie thermique et électrique, semble prometteuse. Julien Brochier de Vivlo mentionne: «Aujourd’hui nous sommes sur des machines hybrides, qui peuvent travailler soit avec de l’énergie thermique, qui va être revalorisée sur des sites industriels car on va aller capter de l’énergie sur des fours des sources d’émission d’énergie, et couplé à une alimentation électrique de l’évaporateur». Cette approche, déjà mise en œuvre sur deux sites en France, permettrait de diminuer la consommation énergétique jusqu’à 80%.
En termes d’installation, Veolia Water STI, avec ses évaporateurs de la gamme EVALED, s’efforce de combiner robustesse et faible consommation énergétique. Frédéric Fuhrmann souligne que «les installations conçues actuellement par rapport à une installation d’il y a 30 ou 40 ans, on a réduit de manière assez conséquente la consommation énergétique». Ainsi, que ce soit via des optimisations techniques ou des approches hybrides, l’efficacité énergétique des évaporateurs continue de s’améliorer, ouvrant de nouveaux horizons pour la durabilité. H2O met également en avant l’importance du prétraitement avec ses évaporateurs sous vide VACUDEST. Grâce à des innovations comme l’Activepowerclean, ces unités assurent un transfert de chaleur optimal par un nettoyage automatique de l’échangeur de chaleur, ce qui réduit les coûts d’exploitation et améliore l’efficacité énergétique. En intégrant la chaleur résiduelle pour préchauffer les effluents entrants, ces systèmes offrent des performances inégalées en termes de durabilité et de fonctionnement écologique.
PASSER À L’ÈRE DES INSTALLATIONS INTELLIGENTES : AUTOMATISATION ET CONNECTIVITÉ DES SYSTÈMES
Les évaporateurs sous vide modernes intègrent des innovations technologiques avancées en matière d’automatisation et de connectivité, offrant un suivi plus précis et une gestion optimisée des processus d’évaporation. Frédéric Fuhrmann de Veolia Water STI souligne que les systèmes actuels sont «entièrement automatisés», assurant ainsi un contrôle rigoureux et une réduction significative des interventions manuelles. Les fabricants ont développé des dispositifs de surveillance à distance accessibles à tout moment en temps réel via des smartphones, PC et tablettes. Ces systèmes offrent la possibilité de suivre en temps réel les paramètres des équipements, avec une passerelle sécurisée garantissant la confidentialité des données. Cette flexibilité permet aux opérateurs de recevoir des alertes instantanées et de prendre rapidement des mesures correctives en fonction des notifications.
Confirmant cette tendance croissante au passage vers la numérisation, JeanLin Laurouaa de Kmu Loft et Julien Brochier de Vivlo évoquent notamment que toutes les machines actuelles «sont suivies sur smartphone en temps réel». Cette avancée technologique permet non seulement une optimisation de la performance des évaporateurs mais aussi une amélioration des capacités de maintenances prédictives. La connectivité à distance permet également la collecte continue de données opérationnelles, facilitant ainsi l’analyse et l’optimisation des cycles d’évaporation. «Nous essayons tous de collecter des informations, afin d’optimiser toujours plus la gestion des machines et de s’arrêter à temps pour éviter des coûts d’exploitation très forts» insiste JeanLin Laurouaa, soulignant l’importance de la gestion des données pour optimiser les performances des évaporateurs sous vide. «Il s’agit d’une offre qui suit la demande du client car les installations sont censées fonctionner 24 H/24 et 7 j/7 . Or, selon leurs activités, les entreprises n’ont pas du personnel mobilisé h24, donc ils ont aussi besoin de pouvoir disposer d’alertes, d’alarmes, de suivi à distance. Cela permet aussi de faire des courbes de suivi à distance, et de manière automatique, ce qui n’était pas le cas auparavant, où il fallait exporter des data sur des tableurs de type Excel afin d’analyser des données extraites. Tout cela a été automatisé, ce qui est une suite logique pour l’industrialisation», ajoute Frédéric Fuhrmann de Veolia Water STI.
Les retours d’expérience montrent que
ces innovations offrent non seulement
un gain en termes de réactivité et de
maintenance, mais qu’elles contribuent
également à une meilleure compréhension des cycles de vie des machines,
permettant des gains en efficacité
énergétique et une réduction des coûts
opérationnels. Tout cela inscrit les évaporateurs sous vide dans une nouvelle
ère numérique, alignée sur les besoins
industriels actuels.
DES SOLUTIONS SUR MESURE : QUAND LA CHIMIE DES EFFLUENTS GUIDE LA TECHNOLOGIE
L’évaporation sous vide s’adapte à une multitude d’applications industrielles en raison de sa flexibilité face à des effluents variés. Jean-Lin Laurouaa de Kmu Loft, précise: «Les évapo-concentrateurs sont certes adaptés à une pollution minérale dissoute et à une pollution organique dissoute, mais en fonction de la qualité des effluents, il convient toutefois de choisir un type d’évapo-concentrateur plutôt qu’un autre. En effet, certains évapo-concentrateurs sont plus adaptés que d’autres pour les effluents les plus corrosifs et acides». Essentielle dans des secteurs comme la microélectronique et le photovoltaïque, où les effluents contiennent souvent des composés agressifs comme l’acide fluorhydrique. Ces applications bénéficient de l’utilisation d’évaporateurs spécifiques revêtus de matériaux résistants à la corrosion. Julien Brochier de Vivlo souligne que pour les flux acides et très corrosifs, les évaporateurs à basse température avec des vides très poussés sont préconisés afin de limiter les phénomènes de corrosion.
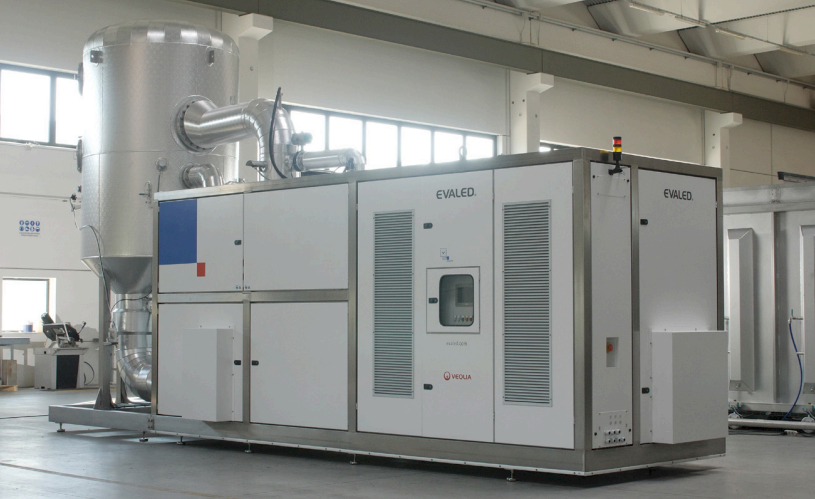
Il mentionne: «Le fait d’être à basse température permet de ne pas toucher à la rhéologie du produit». Ces types d’évaporateurs sont configurés pour des températures d’ébullition autour de 40 degrés, ce qui stabilise le comportement du produit dans la chaudière et les échangeurs. Pour des applications comme celles rencontrées chez Safran ou dans l’industrie du traitement de surface, Dominique Buzare de AFIG'EO Engineering précise que les techniques de compression mécanique sont souvent préférées pour leur faible consommation énergétique: «La compression mécanique qui va prendre le pas (…) avec le prix de l’électricité». Cependant, il souligne également l’importance de protéger les compresseurs contre la dégradation par des composés comme l’ammoniac, en utilisant des techniques de prétraitement adéquates. L’approche de Veolia Water STI est similaire lorsqu’ils traitent des flux avec des composés agressifs.
Frédéric Fuhrmann explique que leur gamme EVALED exploite des revêtements spécifiques et des configurations adaptées pour travailler avec des acides très corrosifs. Veolia se concentre aussi sur la cogénération pour utiliser de la chaleur fatale disponible sur les sites industriels, réduisant ainsi les coûts énergétiques tout en améliorant la robustesse des installations. Bien que 90% de ses installations de ZLD intègren des évaporateurs CMV, Aquaprox I-Tech, de son côté, démontre l’intérêt de la pompe à chaleur dans quelques scénarios où la température doit rester basse pour éviter de dégrader des composés organiques sensibles. Matthieu Delaunay expose: «Parfois aussi, nous préférons travailler avec une pompe à chaleur car on a une pérennité du système due au moindre impact du NH4».
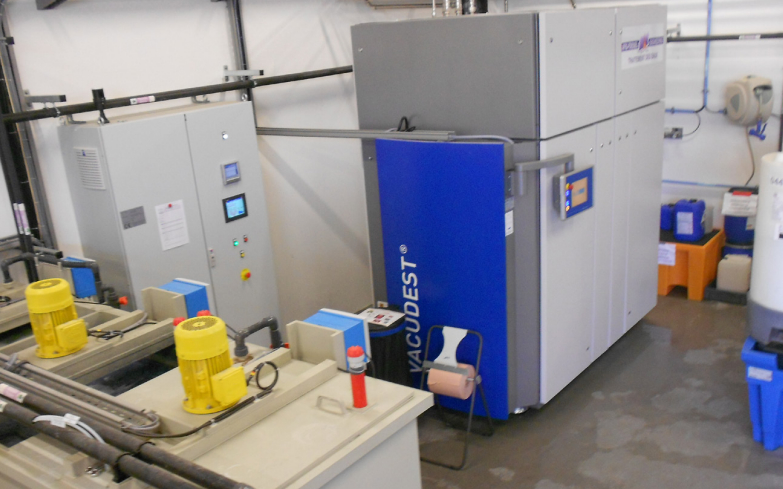
En somme, les choix technologiques
sont guidés par la nature chimique des
effluents à traiter, prenant en compte les
interactions spécifiques entre les composants des effluents et les matériaux
des évaporateurs. Ces méthodologies
adaptées et innovantes permettent aux
industries de traiter efficacement leurs
eaux usées tout en minimisant les coûts
opérationnels et en maximisant la durabilité des installations.
Pour des produits moins sensibles à la
température, Alain Dehay de FE Group
mentionne que la concentration à pression atmosphérique est plus économe,
réduisant ainsi le coût d’investissement.
Cependant, pour des produits plus sensibles ou nécessitant une valorisation
énergétique, des pressions plus basses
sont préférées pour limiter l’impact
thermique tout en assurant une efficacité énergétique optimale.
EVAPORATION SOUS VIDE : UNE TECHNIQUE AU SERVICE DU ZÉRO REJET
Le concept du Zéro Rejet Liquide (ZLD) s’impose de plus en plus comme une réponse stratégique aux problématiques environnementales et réglementaires de l’industrie. Selon Jean-Lin Laurouaa de Kmu Loft, «le zéro rejet coche toutes les cases: en amont moins de prélèvement, et en aval, moins de rejet». Cette approche vise à éliminer complètement les rejets liquides en traitant et réutilisant les effluents sur site, et les technologies d’évaporation sous vide jouent un rôle central dans cette démarche. Matthieu Delaunay d’Aquaprox I-Tech décrit comment l’évaporation sous vide est intégrée dans des solutions globales: «L’idée est d’abord d’avoir des étapes de préparation de l’effluent qui vont aussi par exemple préconcentrer au maximum l’effluent, avec une autre technologie que de l’évaporation». Jean-Lin Laurouaa, lui aussi, souligne l’importance de combiner différentes technologies pour optimiser les coûts opérationnels : «Si les volumes sont trop forts, penser association, combinaison». Les industriels exploitent des avancées récentes en matière d’efficacité énergétique pour rendre les systèmes ZLD plus viables.
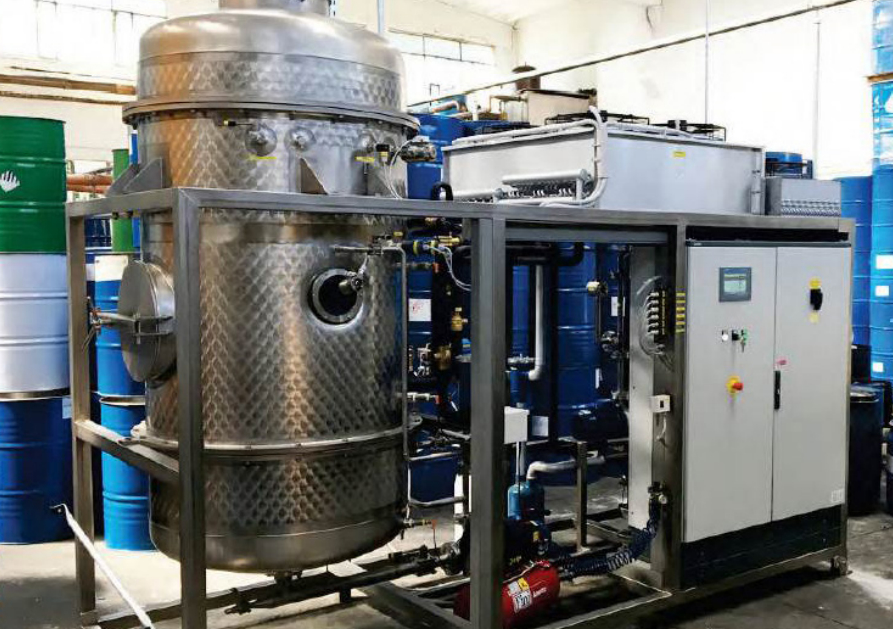
Frédéric Fuhrmann de Veolia Water STI note que «les installations conçues actuellement […] ont réduit de manière assez conséquente la consommation énergétique». De plus, les systèmes modernes bénéficient aussi de techniques d’automatisation et de suivi à distance, comme le précise Julien Brochier de Vivlo: «Toutes les machines aujourd’hui sont suivies sur téléphone portable, suivies en temps réel». Une illustration concrète de l’application du ZLD se trouve dans des industries aussi diverses que l’aéronautique et la micro-électronique. Dominique Buzare d’AFIG'EO évoque l’installation de systèmes complets de traitement de surface avec évaporateurs en Chine et en Thaïlande, et souligne que «l’industriel rejette 16m3 /jour, et l’évapo n’en prend que 1, ce qui fait 100 litres par jour de concentrat».
À l’avenir, les pressions réglementaires et les coûts énergétiques croissants devraient continuer à orienter les industries vers des solutions ZLD. L’intérêt économique et écologique de ces approches se conjugue avec un soutien croissant des pouvoirs publics, comme l’observe Jean-Lin Laurouaa: «Le montant des subventions de l’agence de l’eau est établi en fonction de la qualité d’eau produite et la quantité d’eau économisée dans le cadre d’un zéro rejet. Les projets «zéro rejet» ou REUT sont très souvent les projets les plus dotés (en termes d’aides)».
Toutes les substances qui ont une température d’ébullition plus élevée que celle de l’eau restent dans le résidu d’évaporation. Il s’agit notamment des métaux lourds, des sels, mais aussi des huiles, des graisses ou des tensioactifs. Comme l’eau est évaporée, le volume du résidu de distillation est réduit en moyenne à 5% du volume initial. La vapeur ascendante est pratiquement exempte d’impuretés. Après condensation, elle peut être renvoyée dans le process sous forme d’eau propre. Grâce à cette distillation sous vide, nous sommes en rejet zéro d’eau. Concrètement, le fabricant d’évaporateurs sous vide H2O illustre par exemple l’intérêt de cette solution avec la réalisation d’une nouvelle station de traitement des eaux chez Aluminium Ferri, entreprise située en HauteGaronne spécialisée dans l’usinage, le polissage et l’anodisation, explique Vincent Egmann responsable commercial chez H2O. Sur son site de Givry en Argonne, l’entreprise dispose maintenant d’une unité d’évaporation sous vide CMV VACUDEST de 500 l/h fournie et installée par les équipes de H2O. «L’objectif est le traitement de nos eaux industriels de traitement de surface afin de réutiliser celle-ci et de supprimer notre station de traitement des eaux physico-chimique. Notre objectif était d’aller vers le zéro rejet d’eau, et nous avions un besoin de rajout d’eau de la concession très limité. Avec ce nouvel équipement, Aluminium Ferri apporte une contribution importante à la protection durable de nos ressources en eau potable et investi dans un avenir propre et vivable», explique Michael Huchon, président d’’Aluminium Ferri.
Dans ce cas précis, l’évaporation sous vide s’est imposée comme solution pour traiter les effluents de notre ligne de traitement de surface avec le VACUDEST d’H2O. «Cela nous permet de séparer l’eau propre de nos effluents (résidus), répondant ainsi aux exigences légales. Un autre avantage de ce procédé, c’est que l’eau traitée peut être réutilisée dans notre production. Ainsi, grâce à notre unité d’évaporation sous vide VACUDEST, nous sommes en rejet zéro d’eau et cela contribue à baisser significativement nos consommations d’eau», ajoute-t-il. Pour les industries confrontées aux défis croissants de la gestion de l’eau et des effluents, l’évolution des technologies d’évaporation sous vide offre des solutions puissantes et adaptables. Les innovations en matière de prétraitement, d’automatisation et de consommation énergétique permettent non seulement de répondre aux exigences environnementales, mais aussi de faire face aux coûts opérationnels élevés. La polyvalence des évaporateurs sous vide, adaptable à une multitude d’effluents et capable de jouer un rôle central dans des systèmes de zéro rejet, dessine un futur où durabilité et efficacité convergent.